In Mining Industry 4.0 Translates to APM 4.0
Posted: August 18, 2020
Industry 4.0 dominates the industrial Digital Transformation dialogue and mining companies often wonder, “What does Smart Manufacturing mean for me?” Granted, it’s an initiative conceived to advance discrete manufacturing. While auto, electronic, aviation, and similar industries produce smart connected products made from bills of materials (BOMs), mining, metals, and minerals products aren’t connected to anything and they’re certainly not “smart” (e.g. don’t contain embedded technology or connectivity).
Consider this: the mining industry has been talking about “mine of the future” (MOF) for over a decade; early adopters called it “the digital mine.” The industry is obviously looking to Digital Transformation as a way to improve operations and productivity. The answer mining enterprises seek is still within Industry 4.0, but in context of what LNS Research calls APM 4.0. Mining, metals, and minerals companies are asset-intensive businesses and have long focused on asset performance management (APM) as a core competency. As Industry 4.0 has transformed discrete manufacturing, APM 4.0 is transforming asset-intensive industries like mining.
APM 4.0 So Much More Than a “New Breed” of APM
Tech vendors have (inadvertently) conditioned the business and industrial world to think of any new software version as just an evolutionary step; going from version 1.0 to 2.0 to X.0 is simply adding a few new features or functions, or maybe updates the user interface. LNS Research defines APM 4.0 as far more than just a technical evolution of the computerized maintenance management system (CMMS) or condition-based maintenance (CbM) tools, or even the adoption of reliability-centered maintenance (RCM) in a predictive maintenance (PdM) model.
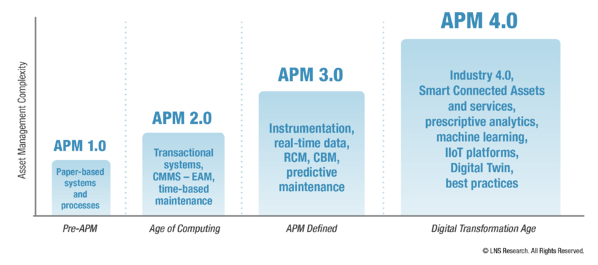
APM 4.0 is a step change in the way a company conducts maintenance. Just as with Industry 4.0, APM 4.0 relies on cyber-physical systems to fundamentally change the way a business works. APM 4.0 relies on a set of critical technologies:
• The Industrial Internet of Things (IIoT)
• Big Data analytics
• Predictive analytics leveraging artificial intelligence (AI) and machine learning (ML) coupled to modeling and simulation
• Mobility to serve up information anywhere on any device
• Augmented reality / virtual reality (AR/VR) to present information in an enhanced user experience
Just as with Industry 4.0 you can’t buy APM 4.0. You build it by mashing together the critical technologies to create digital twins of the assets, systems and value chains across a company and industry.
Digital Twin Transforms Mining
A Digital Twin, in the APM 4.0 sense, is so much more than just a piece of equipment’s engineering design documents. A true Digital Twin is a digital representation of an asset or a system of assets that starts with the original engineering design and carries forward to include the digital image of how a piece of equipment has been operated in the past, is currently operating, and most importantly, through simulation and modeling, might operate in the future. Digital Twin opens up a whole new set of opportunities:
• Reconcile actual ore body concentration against geotechnical models
• Understand operator impact of productivity and equipment operating costs to drive higher profitability
• Modify block plans to facilitate consistent margin as prices vary
• Reduce MRO spend by altering operating profiles
• Improve safety through enhanced training
• Autonomous operations
The new opportunities compound the more traditional and expected improvement value such as:
• Reduce downtime, increase uptime, higher reliability
• Improve planned to unplanned maintenance ratios
• Reduce energy costs
• Boost delivery performance
Think Profit Optimization, Not Production Optimization
While it usually holds that producing more leads to higher profits, it isn’t always the case. Over maintaining equipment can result in equipment being out of service more often than necessary and incurring higher maintenance costs than warranted. This predicament can happen when a simplistic CBM model detects a trend in the equipment’s performance that has, in the past, indicated a potential future failure. In reality, the problem might have happened because the company ran the equipment beyond its normal operating mode for a short period of time, so experienced accelerated wear. Once returned to normal operation the wear returns to a level that no longer requires an accelerated schedule.
With an APM 4.0 Digital Twin, the mining enterprise examines the entire environment in context, not just as a snapshot in time. The Digital Twin shows the potential impact of an operating change on equipment reliability and maintenance costs. To illustrate the concept let’s consider how distribution companies have given truck drivers immediate feedback on how they’re driving the truck and the way it impacts costs. The practice has dramatically reduced maintenance costs, improved tire life, and simultaneously allows for meeting production goals.
Mining companies that desire a similar approach use AR/VR simulations for a better learning environment and more impact. APM 4.0 enables this type of fidelity throughout all operations. With robust digital twins across all mining operations, training can go beyond maintenance staff and first level operators. Supervisors can explore all kinds of operating models and plant management scenarios. It also opens the door to test and practice disaster and event readiness, like reacting to hurricanes, severe accidents or other situations they never encounter in the course of “daily business,” and understand how they conduct business in the face of these events.
Real-World Data = Better Training
Another parallel for disaster planning and training for plant supervisors and managers in mining is airline pilots. Pilots spend many hours in simulators practicing how to handle one engine landings, pressure losses and other calamities even though most of them will never encounter any of those conditions in their career. However, stories like the one when Captain Sullenberger landed US Air Flight 1549 on the Hudson River after bird strikes took out both engines show the immense value of that training. So too can mining operations plant managers learn how to handle the unexpected.
Use cases like these clarify that Industry 4.0 isn’t “just” for discrete manufacturers. In fact, the value and impact of Digital Transformation (in the form of APM 4.0) is likely much more profound for mining, metals, and minerals companies than their industrial counterparts in product manufacturing.
To learn how AVEVA software can drive profitability in mining view our mining solutions page.
Related Blog Posts
Stay in the know: Keep up to date on the latest happenings around the industry.