Armstrong World Industries needed real-time production line data, easily visualized and accessed from the manufacturing floor. So it used AVEVA™ InTouch HMI web client with customized process and maintenance screens and decreased production changeover time, decreased scrap, and increased throughput. This end-to-end real-time visibility has enabled operators to move from a reactive maintenance strategy to a proactive strategy and act on emerging issues before they become downtime events.
Challenges
Lack of visibility into operational data on the plant floor
Bringing IT and OT sources into the same solution
Cost and time to deploy across the business
Results
21%
reduction in changeover time on one line
6 hours
additional capacity created by an average changeover reduction of four minutes
7,500ft2
overall throughput gain from identifying and fixing an issue with one of the feeders
0.25%
scrap reduction through faster real-time information of scrap causes
Putting live process data in the hands of line operators on the floor
One of the challenges Armstrong faced was that no one on the production line could easily see how the equipment they were responsible for was performing. The company had been using AVEVA InTouch HMI since the early 2000s. Local HMIs mounted on equipment told operators that the conveyors and equipment were running, but not how they were running. Operators needed access to real-time production data. With the rollout of AVEVA InTouch HMI web client, the company saw an opportunity to further automate its plants and gain better visibility into real-time production data on the shop floor.
The team worked with the operators who use this equipment to determine what would be most helpful for them to see in the plant’s equipment dashboards. What were the specific issues and challenges operators faced on the line? What data could help them operate more efficiently? How might that data be best visualized? New displays and monitoring screens, now quickly and easily made with AVEVA InTouch HMI, reflected this operational insight.
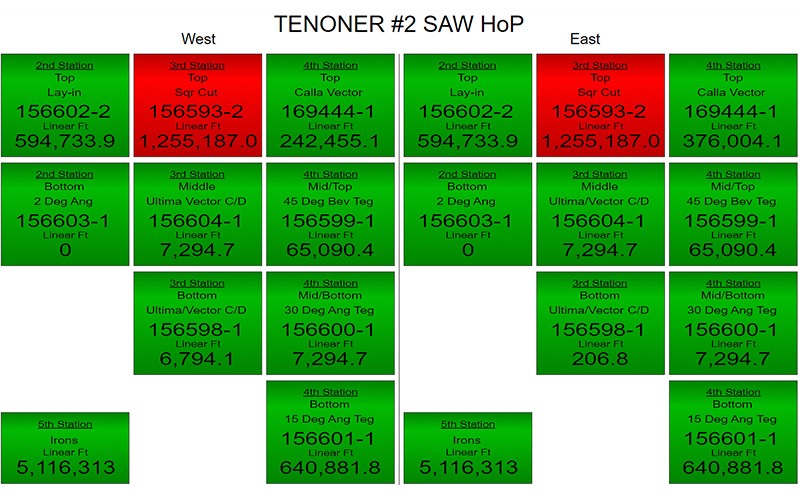
End-to-end real-time visibility for data-driven decisions
Sensor-based tracking on equipment now allows operators to see in local customized dashboards how the product is flowing on the line. Operators and supervisors can see the gap between tiles, the position of the tiles, and if they’re skewing. Customized process and maintenance screens are now on the shop floor, where operators can quickly access and act on critical equipment information. Screens show blade life, for example, so that operators know when it’s time to change a blade before a product quality issue causes downtime. Operators have immediate access to paint storage details, such as the age of the paint and how much of it is left. Supervisors can compare the last five runs on the line to identify common downtime causes and anticipate maintenance needs. This newfound visibility translates to less downtime and more efficient operations.
The architecture of the solution is simple and scalable. Armstrong centralizes disparate information from PLCs, Excel spreadsheets, and other databases into the single AVEVA InTouch HMI interface. The information then comes out in HTML5 web pages. Now, all users need to access key production line data in AVEVA InTouch HMI is a browser connected to the internet. Users can simply open a browser and select the server running AVEVA InTouch HMI using Windowviewer. Custom security settings control permissions, so that a user can either have access to read only or read and write. This configuration allows users to access production data wherever they are, and even make a change on the line without having to be physically present.
Solution
AVEVA InTouch HMI web client for real-time production line data across all mineral fiber manufacturing sites
A 20% decrease in production changeover time
Previously, operators on the shop floor didn’t know when a production run had started, where it was in the process, or how long it had left. Now, countdown timers for item changeovers show supervisors and operators exactly how much time is left before machine settings and materials need to be switched for a new product. Crews can get everything they need for an efficient changeover prepared beforehand. They can quickly see when something is amiss ahead of time and aim resources at solving the problem.
In 2017, Armstrong invested in a brand-new line that allowed it to produce different sized tiles. Before this, the company’s production runs were long, as they were working with just two different tile sizes. But with this new line, there were many different widths, lengths, different paint, and different edge profiles. On this line alone, there were 80-130 changeovers a month. After implementing these new countdown screens, the line saw a 20% decrease in changeover time. The average time required for a changeover decreased from 19.76 minutes to 15.66 minutes, and the line gained over six hours of additional capacity.
“We no longer needed to wait for a production summary each hour to know if any changes had been successful. We now know within five minutes.”
—Joe Alba, Value Stream Manager, Armstrong World Industries

Proactive maintenance and scrap reduction
By identifying inefficiencies in the production process, operators and maintenance crews can now implement process improvements and engage in predictive maintenance to reduce scrap rates. Overall, the implementation of new monitoring screens has resulted in a 0.25% scrap reduction across Armstrong’s manufacturing plants.
Real-time data about how equipment is performing helps maintenance teams identify other mechanical inefficiencies early. For example, the performance of one of Armstrong’s feeders, when it was running, was trending down. Operators saw this and called maintenance, who identified a mechanical issue with one of the valves. They immediately fixed the issue, gaining about 7,500ft2 an hour in throughput.
In another example, one of Armstrong’s production lines, an older line, didn’t even have a local HMI screen, nothing that showed operators how the equipment was performing. Operators would have to walk two minutes to look at the HMI screen to get basic production information. Within one day, the team developed and deployed an AVEVA InTouch HMI web client screen displayed on a 75” TV that showed all item changeovers. Suddenly operators could see how production was going on the line, which enabled them to cut inefficiencies in changeovers and act quickly when an issue arose. This deployment was simple to roll out: all they needed was a TV, power, and network access.
“We had wanted this in the lamination area for years but costs were restrictive, the speed which this was operational to us was impressive. It really helps the workers in that area.”
—S. Campbell, Electrical Engineer, Armstrong World Industries
The implementation of these new monitoring screens has encouraged a culture change at Armstrong World Industries. Instead of reactive maintenance, operators are proactive. Real-time process visibility allows them to take action before an emerging issue becomes a downtime event. Supervisors and operators can VPN in anywhere in the world. They’re not limited to being in the plant. Now, Armstrong’s customers can have faith that they’re getting the best quality product, while behind the scenes, Armstrong’s operators use smart real-time production data to ensure that faith continues.
Product highlights
AVEVA InTouch HMI, formerly Wonderware
Formerly Known As InTouch HMI
AVEVA InTouch HMI is HMI visualization software for operators to achieve real-time operations visibility. The world’s most widely used plant HMI for process monitoring and control.