Are you ready to join Generation i?
A new generation is rising, defined not by age or experience, but by the relentless desire for progress.
By harnessing trusted insight and ingenuity - your Industrial Intelligence - you can open up new avenues for growth, drive decarbonization, and reshape Manufacturing today and for the future.
Maximize agility to meet customers' needs, while boosting efficiency and growth, through trusted insights that span your ecosystem.
Read how AVEVA customers harnessed their Industrial Intelligence
- New Belgium Brewing
- Pfizer
- Henkel
New Belgium Brewing’s Industrial Intelligence turned insight into impact
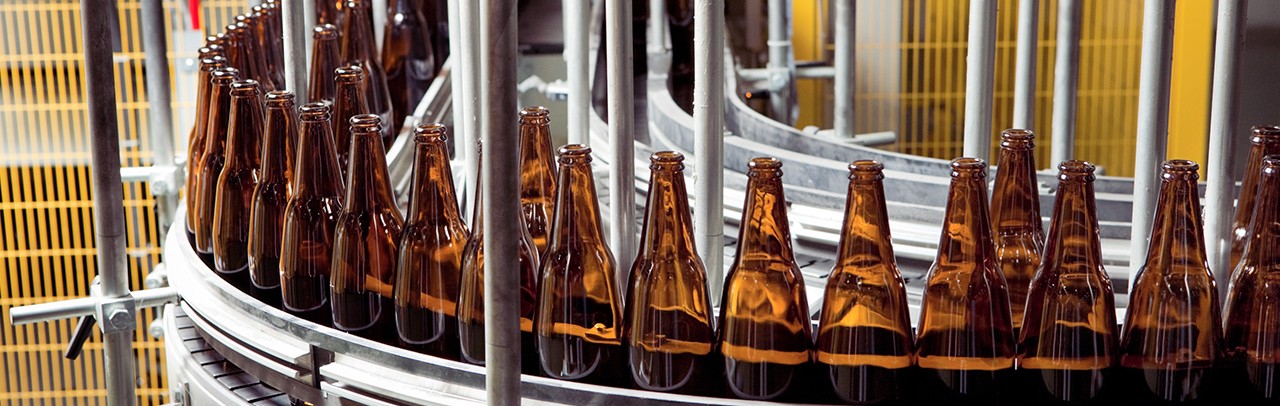
New Belgium Brewing Co., based in Fort Collins, Colorado, produces some of the world’s most popular craft beers.
To ensure its beer-loving fans continue to receive the highest quality beverages, New Belgium needed to streamline and improve its brewing and bottling operations.
New Belgium’s brewing operations were rapidly reaching capacity, and we needed to identify both efficiencies and inefficiencies in our bottling lines so the brewery could maintain its operating schedule.
The brewery faced three key challenges:
- Need for real-time information on unscheduled downtimes to reduce production slowdowns.
- Need to address gaps in methods and processes to streamline production.
- Need to drive consistency across multiple production sites and environments.
Real-time insight leads to increased production and efficiency
An audit of its production line revealed that New Belgium was losing valuable packaging time during both scheduled and unscheduled downtimes. Its existing manual data recording process was not capable of keeping up with the level of bottling production New Belgium needed to achieve.
The brewery’s existing systems provided huge amounts of data, but without context. The implementation of AVEVA Manufacturing Execution System now meant that it could effectively collect and analyze that data to turn it into actionable real-time insight. With greater visibility and a true understanding of actual production capacity for predictable order fulfilment, New Belgium can maintain its production and sales targets.
Enhanced visibility and real-time insights have enabled the brewery to reduce downtime by 50%. The combination of AVEVA Manufacturing Execution System with the brewery’s existing installations of AVEVA InTouch HMI and AVEVA System Platform have also enabled New Belgium to drive process improvements through automation. The brewery achieved an increased in OEE from 45% to 65% in 2 years.
Multiple sites, same impeccable flavors
When New Belgium acquired two new brewing sites at different stages in their automation journeys, it created a new challenge of producing 100% flavor-matched beer across all sites. The brewery found its solution in AVEVA Operations Control. The solution has enabled New Belgium to pilot and test strategies at one site before implementing at others. Rather than needing to have the perfect strategy devised at the outset, the brewery can learn what it needs as it progresses.
Tapping the future
New Belgium Brewing has harnessed its industrial intelligence to provide the agility it needs to maintain a tradition of excellence even in an ever-changing business environment.
Pfizer's Industrial Intelligence turned timesaving into lifesaving
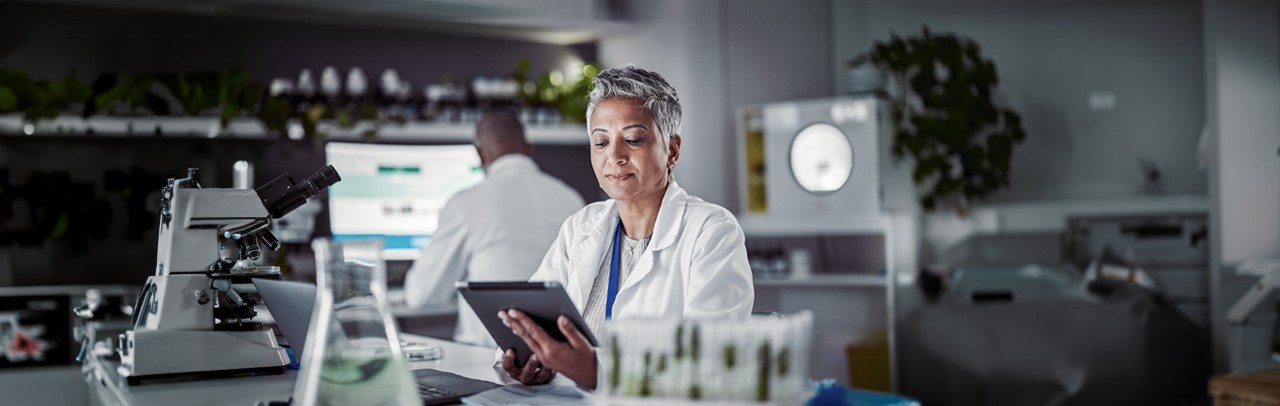
Pfizer relentlessly pursues breakthroughs that change patients’ lives, and its teams drive innovation to make the world a healthier place. This dedication shone brightest when the call came for the COVID-19 vaccine.
With the world waiting, Pfizer embarked on compressing the vaccine development timeline from nine years to nine months. Achieving this required re-invention and feats of innovation in science as well as data management and process optimization.
Having already embarked on a digital transformation journey with AVEVA, Pfizer understood the transformative potential of standardized and centralized data management to unlock benefits throughout its value chain.
When COVID-19 emerged, Pfizer swiftly leveraged these established practices to accelerate the vaccine project, recognizing the pivotal role of AVEVA software in this endeavor.
We were convinced that science would win, and how data and the AVEVA PI System would be an important part of that victory.
Innovating at the speed of light
Pfizer streamlines operations, facilitates collaboration, and accelerates decision-making across its network by centralizing and standardizing data collection and analysis.
The AVEVA PI System serves as the cornerstone of Pfizer's Global Historian Program, providing real-time, full data visibility and control over its manufacturing processes.
This optimizes Pfizer’s operations, supports the transfer and sharing of data, empowers collaboration between different sites, and enables rapid adaptability.
The data foundation enabled by the AVEVA PI system allows for the monitoring of critical parameters, such as temperature control in freezer farms, mRNA concentration in vaccine batches, and production scheduling for capacity modeling and the removal of bottlenecks.
Additionally, Pfizer’s team can gather insights on process performance, identify areas for improvement, and ensure batch quality and compliance with regulatory standards.
Leveraging the scalability and flexibility of AVEVA’s software, Pfizer exceeded expectations and delivered an unprecedented 3.2 billion doses of the vaccine by the end of 2021.
Transforming medicine manufacturing
By putting industrial intelligence to work, Pfizer maximizes the benefits of advanced data management and analytics.
Harnessing data to accelerate vaccine development has the potential to save millions and restore hope during global crises.
And centralizing data, standardizing processes, and leveraging predictive analytics can streamline operations, reduce time-to-market, and improve the efficacy and safety of medications.
By bringing it up to the global historian, and structuring it in a consistent fashion, suddenly we were able to leverage our SMEs throughout the world.
Henkel's Industrial Intelligence turned data into savings
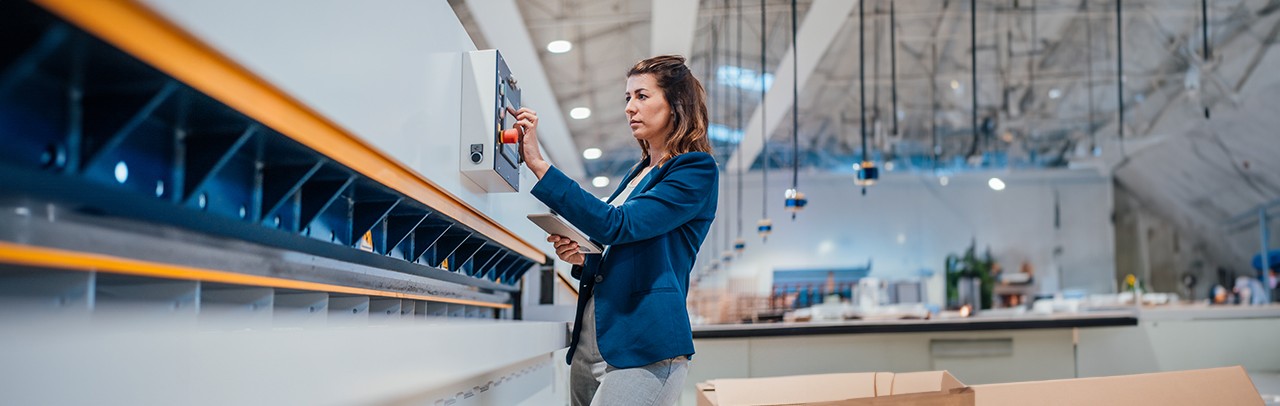
Henkel, a global FMCG manufacturer, is a pioneer, reimagining and improving life today and for generations to come. This spirit led to the digital transformation of their Laundry & Home Care division to drive greater efficiency, and thereby greater sustainability.
Goals included reducing specific energy consumption, achieving ISO 50001 certification, and improving supply-chain resource efficiency by 5–6% annually, all the while maintaining growth.
However, Henkel’s challenges in data collection and communication across the supply chain would make attaining its goals difficult. A partnership with AVEVA led to an effective solution.
We adopted a digital backbone as this facilitates a vertical approach. It’s faster and ensures application roll-out quickly generates tangible business benefits.
An elegant device-agnostic solution
Henkel uses AVEVA software to enable its teams to capture and contextualize operational data, manage domain, database, application programs. Device integration is configured independently, without affecting the architecture. Engineers can seamlessly incorporate legacy hardware.
Teams installed more than 4,000 physical and virtual sensors, and more than one million data points are captured every day. Touch-screen devices instantly consolidate and contextualize relevant data, enabling operators to collaborate in real-time and identify problematic areas.
Now, operators can accurately measure energy use across the entire factory. They analyze results within meaningful parameters, empowering teams to take corrective action and reduce energy consumption.
AVEVA’s software delivers overall equipment efficiency (OEE) data that further increases productivity. Machine downtime information enables operators to target in-line improvements.
Payback and then some
Energy consumption decreased by 16% in 2020, leading to €8 million in annual savings and €37 million saved to date. The project achieved full payback within four years and quadrupled ROI after eight years.
Other benefits include a 15% improvement in overall equipment effectiveness (OEE), reduction of filling line waste and 100% label quality rate.
By putting industrial intelligence to work, Henkel transformed its Laundry & Home Care operations, driving sustainability and efficiency across its value chain.
Once we’d implemented the AVEVA-based EMS solution, the energy saved was equivalent to the capacity needed to support the three million inhabitants of Amsterdam and Vienna
AVEVA Industrial Intelligence Index
The AVEVA Industrial Intelligence Index is your guide to navigating the trends and transformations shaping the manufacturing sector.
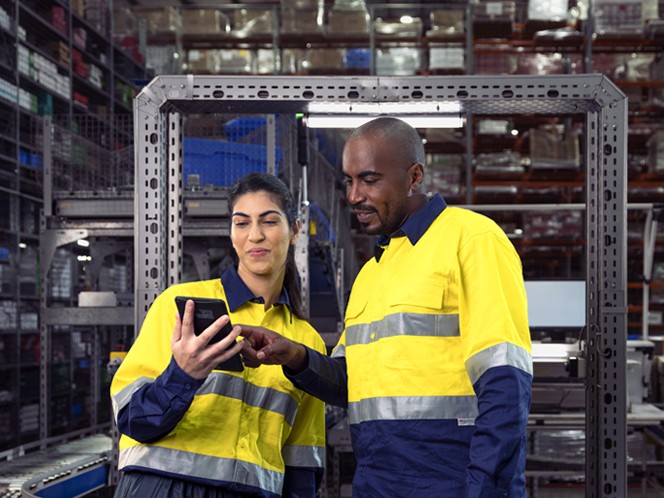
Explore more
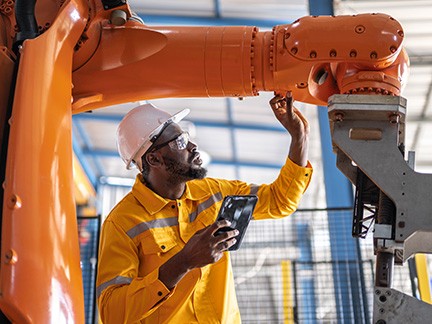
Digitally transforming operations
AVEVA provides a wide range of digital manufacturing solutions for companies aiming to modernize and digitally transform their manufacturing operations.
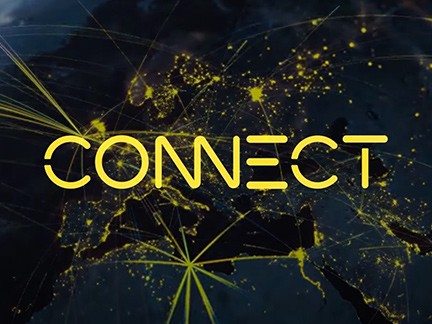
Get the CONNECT Effect
CONNECT, our industrial intelligence platform, empowers you with trusted intelligence and actionable insight to optimize performance and drive sustainable growth. Put the CONNECT Effect to work for you today.
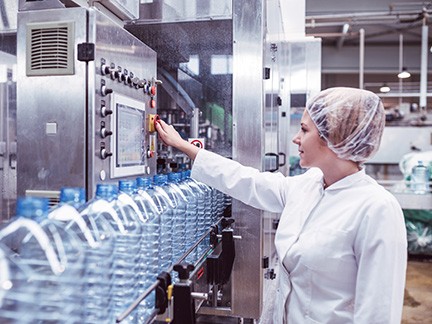
Delivering impact for industry
AVEVA builds industrial software solutions that empower you to innovate. Discover our work in Manufacturing.