Modular construction: the background to the boom
Posted: May 02, 2025
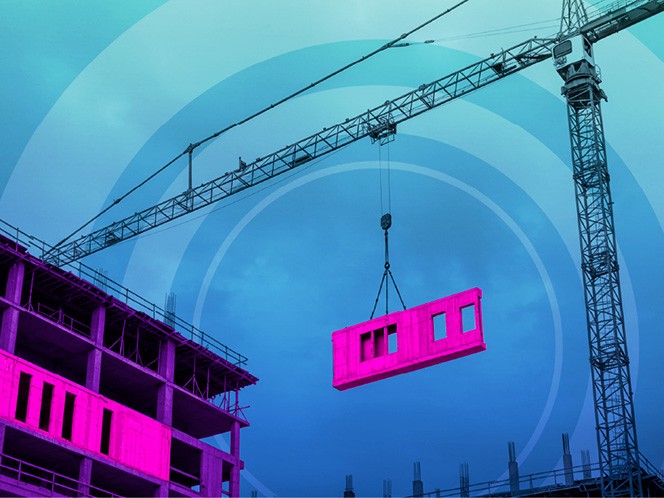
What do Roman forts, the Eiffel Tower, American roadside diners, and the world’s northernmost liquefied natural gas project have in common?
The answer is modular construction, an approach that brings production efficiencies to bear on buildings by manufacturing or prefabricating (usually standardized) components. And it is having a moment.
Enabled by increasingly globalized supply chains and advances in industrialized production, modularization presents a way to generate cost savings and increase flexibility for construction projects of all sizes. As the World Economic Forum recently noted, it can also help to achieve circularity in the construction industry by reducing waste, promoting sustainable resource cycles, and allowing components to be reused and repurposed. One McKinsey report suggested that modular construction has the potential to save up to 20% of total costs and to shorten a project timeline by up to 50%, in part by reducing on-site work requirements.
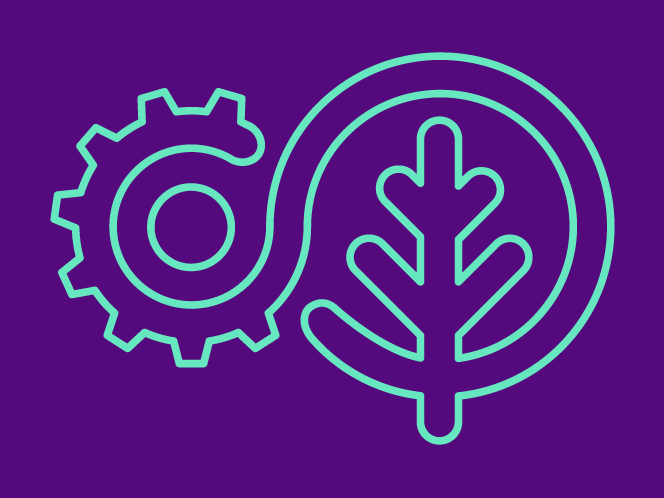
Our Industrial Life
Get your bi-weekly newsletter sharing fresh perspectives on complicated issues, new technology, and open questions shaping our industrial world.
Major construction players like Skanska, Laing O’Rourke, and Bouygues have all invested in modular construction. In 2012, Broad Sustainable Building made headlines by constructing a prefabricated 30-story hotel in China in just 15 days, as did Chick-Fil-A with its time-saving modular restaurant building initiative that began in Roswell, Georgia, in 2020. And modularization has been adopted by players in the EPC (engineering, procurement, and construction) market, too, such as McDermott with its fully modularized Woodfibre LNG project in British Columbia in addition to Technip and its partners when building the Yamal LNG facility in the Arctic far north.
Modular construction is sometimes seen as cutting-edge or even futuristic. But this approach to construction has deep roots in industrial history. In this first part of our two-part series, we will dive into that history. In part two, we will reflect on what the trend towards increasing modularization could mean for EPC firms operating today.
Early history of modular and prefabricated construction
Some aspects of modular and prefabricated construction are almost as old as human society itself. Nomadic cultures built shelters that were easily dismantled and transported—think Mongolian gers. In Ancient Rome, soldiers were trained to build wooden forts that had been prefabricated in pieces small enough to be carried around the empire and then quickly assembled, thus enabling the defense of newly conquered territories.
During the medieval period, pre-cut wooden elements were used in the construction of temples in Japan and of houses across Europe. In 1624, a disassembled building was shipped from England to Cape Ann, Massachusetts to provide a familiar kind of shelter for a newly arrived fishing fleet.
Yet it was in the 19th century, in the wake of the Industrial Revolution, that modular construction really took hold. On the one hand, advances in mechanized production and transportation were bringing new efficiencies to offsite manufacturing. On the other hand, European colonialism and later the Gold Rush drove demand for cheap, standardized buildings in hard-to-reach locations. In the 1830s, the English carpenter Herbert Manning began selling a wooden “Portable Colonial Cottage,” whose numbered parts were manufactured in his London workshop, then transported by ship to their destinations, typically British colonies in Australia and South Africa. Manning would later expand his offerings; other manufacturers joined in too, boosted especially by the availability of mass-produced corrugated iron and rising demand in California.
Industrialization also saw the rise of modularized construction for non-residential purposes. The English used prefabrication to erect barracks, hospitals, and supply depots during the Crimean War, most famously the Renkioki Hospital in modern-day Turkey. London’s Crystal Palace was also erected in a modular fashion.
But modularization reached new heights, so to speak, with the 1889 construction of the Eiffel Tower. Gustave Eiffel had 18,000 iron elements prefabricated in his factory on the outskirts of Paris then brought to the Champs de Mars for assembly; the concrete foundations were built in just five months and the metal tower put up in under two years. The spectacle provoked both excitement and disgust among Parisians. An 1887 protest letter in the French newspaper Le Temps asked: “Will the city of Paris continue to associate itself with the bizarre and mercantile imaginings of a machine builder, thereby disfiguring itself irreparably and dishonoring itself?"
Monsieur Eiffel was vindicated. His tower, initially temporary, received two million visitors during the 1889 World’s Fair and soon gained permanent status as France’s most iconic building.
20th-century prefabrication: rise, decline, and revival
“By the turn of the twentieth century, architects and inventors had developed prefabricated houses of nearly every material—timber, concrete, sheet metal, and cast iron—all meant to be produced in great number, many subject to patent,” write art historians Barry Bergdoll and Peter Christensen.
The United States and Europe were entering the era of the kit house, which could be chosen from a catalogue and ordered for delivery with almost all the materials required for self-assembly. The U.S. firm Sears, Roebuck, and Company heavily invested in the concept, ultimately selling around 75,000 kit houses between 1908 and 1940.
Prefabricated architecture peaked in popularity after the Second World War. Postwar conditions in the U.S. and Europe meant the need for speedy reconstruction and the rapid expansion of social housing, while both steel and skilled construction labor were in short supply. Mass production techniques and industrial infrastructure from the war could be repurposed for residential uses, promising major economies of scale. Architects, engineers, and urban planners were also able to further develop earlier modular initiatives and assembly-line-inspired product experiments by the likes of Buckminster Fuller—who declared he wanted to create “houses like Fords.”
Modular building produced a quick and economical housing supply, especially for low-income people. American suburbanization, too, was enabled by the availability of affordable precut standardized housing designs. The project city of Levittown—where, in 1950, a Time reporter marveled at how full houses were being assembled at the rate of one per fifteen minutes—used prefabrication to throw up suburban tract homes. In the UK, nearly 500,000 ”prefab” cottages were built in the first decade after the war.
Yet overall—with the exception of Japan and Scandinavia—the reputation of modular construction ultimately fell on account of its association with low-cost and often low-quality housing: the American “mobile home,” the English prefab bungalow, or the large gray prefabricated estates of Plattenbau in East Germany and Panelák in Czechoslovakia.
Despite its fallen reputation, modularization was still used for commercial purposes in the US and Europe. One notable triumph of commercial prefabrication is the American roadside diner—a piece of modular cultural heritage on par with the Eiffel Tower, one might say.
Recently, modularization has been returning to the public eye in a major way, perhaps because we are yet again in a moment where manufacturing technology is advanced and the need for new housing and infrastructure is urgent. In the second part of our investigation, we will look at the advantages and disadvantages of modular construction for EPCs in the present day.