The rise of reshoring
Posted: June 30, 2025
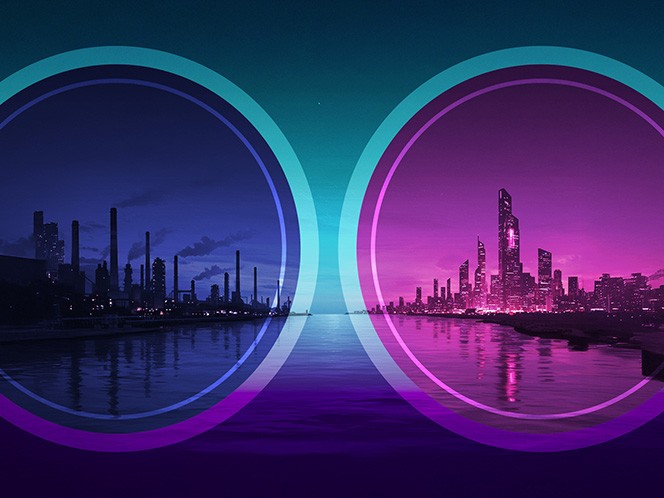
Recently, more and more manufacturers are moving their factories closer to home. A recent Capgemini report showed that in January this year, 56% of executives surveyed from across the U.S. and Europe said that their organization had invested in either nearshoring or a combination of reshoring and nearshoring their manufacturing.
Historically, offshoring was a way for companies to cut costs, usually by moving to countries with lower costs of living and consequently lower labor costs, cheaper raw materials or better tax benefits. Today, many companies see these benefits as secondary to the need for resilience, flexibility and reliability in the face of geopolitical instability, supply chain pressures and increasingly stringent sustainability regulations. As companies move their manufacturing to either neighboring countries or back home, they’re also finding that increasing use of AI and automation can help offset the costs of the move.
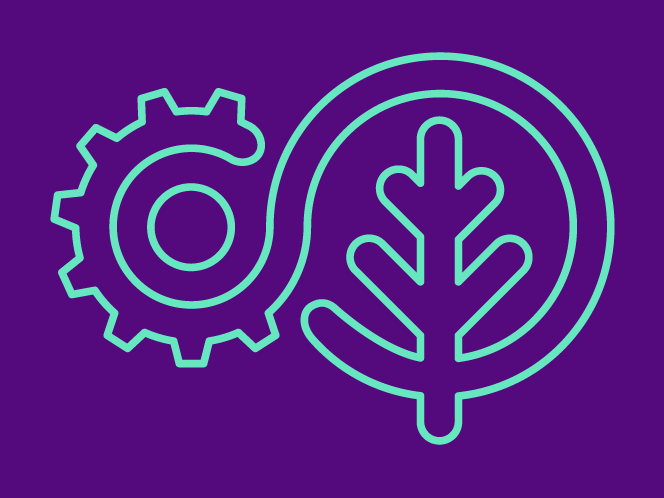
Our Industrial Life
Get your bi-weekly newsletter sharing fresh perspectives on complicated issues, new technology, and open questions shaping our industrial world.
Supply chain pressures and regulation drive reshoring
For many organizations in Europe and the U.S., a desire to reduce lead times, avoid supply chain disruptions, and navigate the impact of regulations and tariffs is encouraging the nearshoring and reshoring trend. Manufacturing closer to home also gives businesses greater control over their products and brings them closer to their customers.
In 2025, 95% of executives said that supply chain pressure was a key driver of their organizations’ reindustrialization, following an increase in supply chain disruptions in 2024. More than half of executives reported that they were reducing their reliance on Chinese products and were prepared to pay a premium to produce in domestic markets.
In Europe, regulation is also driving nearshoring: the E.U.'s Carbon Border Adjustment Mechanism taxes carbon-intensive goods entering the E.U. Near- and reshoring can help companies keep better track of their sustainability goals, reducing the emissions caused by shipping products around the globe and giving them greater control over their manufacturing facilities’ emissions.
Of course, moving production to countries with higher costs of living can mean an increase in labor, land and infrastructure costs, as well as raw materials. Nearshoring can help companies achieve the best of both worlds by alleviating supply chain problems by bringing manufacturing closer to home, while still keeping costs down. For example, for U.S. businesses, nearshoring in either Mexico or Canada can be more cost-effective than moving production back home.
Reshoring and nearshoring in practice
In Europe, car manufacturers have begun moving their electrical vehicle production away from China. Earlier this year, Swedish automotive manufacturer Polestar announced its first electrical vehicle to be built in Europe, the Polestar 7.[1] With most of its sales in Europe, the company is reducing its reliance on Chinese manufacturing and moving production closer to its key customers.
Last year, Volvo also began to shift production of its EVs to Belgium as part of a similar strategy to build its cars where they sell best. To make EX30 production possible in Ghent, the company made investments worth around €200 million to upgrade its Belgian facility. Wide-ranging changes to the plant include the addition of a completely new car platform, the installation of almost 600 new or refurbished robots, an extension of the battery hall, a new door production line as well as a new battery pack assembly line. Between its Swedish and Belgian facilities, Volvo now builds 10 of its electric and hybrid models in Europe. Stefan Fesser, Manager of Volvo’s Ghent plant, said that the company was able to make the move in record time thanks to technology: "New technology and innovation enable[d] us to react more flexibly to market demands.”[2]
Last year, British pharma company GSK announced an investment of more than £200 million to strengthen its manufacturing network in the U.K. The cash will be spent upgrading its existing manufacturing site in Scotland, and constructing new facilities and assembly lines.[3] Elsewhere in pharma, Roche, Eli Lilly, Novo Nordisk, Johnson & Johnson, Novartis, AbbVie, Gilead and Bristol Myers Squibb have announced a combined $200 billion of investments in U.S. manufacturing facilities.[4]
In February, Apple announced it would spend more than $500 billion over the next four years, expanding its facilities in Michigan, Texas, California, Arizona, Nevada, Iowa, Oregon, North Carolina, and Washington. It also plan to build a new factory in Texas. Its new 250,000-square-foot facility will assemble servers that it previously manufactured outside the states.[5]
Can technology ease the transition?
In today’s increasingly volatile world, it seems cost is no longer the most important consideration for many businesses. While businesses consider this transition, some are finding that having an up-to-date digital strategy is helping them ease this transition and reduce the costs associated with reshoring. Capgemini reported that 54% of organizations have already saved more than 20% on costs by using digital technologies in their reindustrialization efforts.
Manufacturing facilities that use technologies such as digital twins, data analytics and AI can reduce costs by improving their monitoring, streamlining operations, and enhancing productivity. Look out for part 2, where we will explore how companies can set themselves up for success with a digital framework that ensures their operations run efficiently.
[1] Polestar 7 will be a premium compact SUV from Europe
[2] Volvo shifting EV production to Belgium to avoid China tariffs, The Times reports;
Volvo Cars starts production of best-selling EX30 electric SUV in Europe
[3] GSK plans to invest over £200 million to improve its UK sites
[4] Rebuilding pharma supply chains
[5] Apple will spend more than $500 billion in the U.S. over the next four years