Will artificial intelligence amplify the case for integrated digital assets?
Posted: July 11, 2025
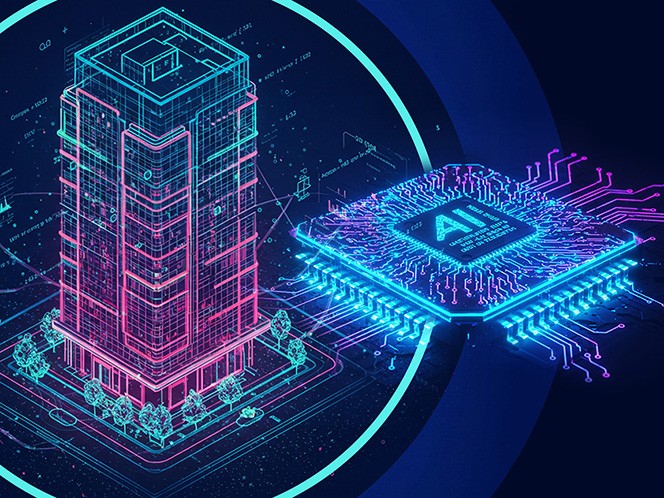
Information handover has long been a challenge in the relationship between Engineering, Procurement and Construction firms (EPCs) and Owner-Operators (OOs). In a 2017 AVEVA survey, a vast majority of OOs reported that poor handover was causing unexpected delays and costs. In many cases, information transfer would only be considered towards the end of the engagement, leading to a single “data dump” of documents from a contractor. Even 60% of those OOs who had defined and agreed on information standards were still unhappy with the information they ended up receiving.
Recently, numerous EPCs have been shifting toward an approach based on data continuity, with the huge amount of engineering information generated during the design and construction phases considered vital for the asset’s startup and operations. Not only are OO data needs being specified earlier; many OOs are now engaging EPCs to hand over a digital twin alongside the physical asset, with the data-rich virtual duplicate becoming part of an EPC’s offering. Virtual assets like digital twins can offer a continuous thread between the pre-design, design, construction and/or operations phases, reducing IT costs and enabling next-level business insights.
This shift toward integration is likely to be accelerated by developments in artificial intelligence, with AI-driven tools bolstering the capabilities of digital twins that draw on data from multiple project phases.
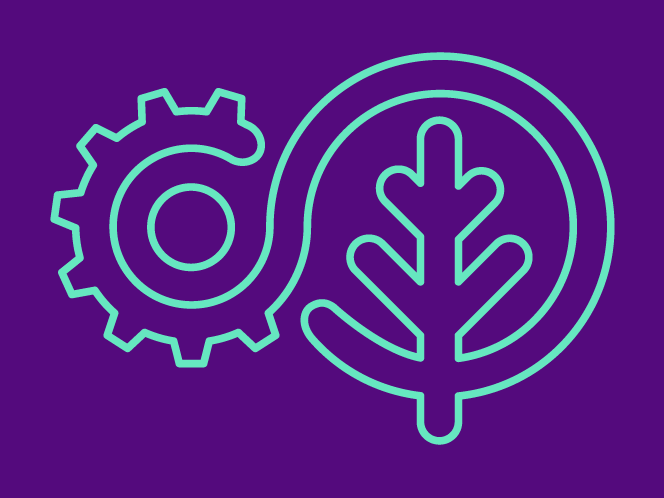
Our Industrial Life
Get your bi-weekly newsletter sharing fresh perspectives on complicated issues, new technology, and open questions shaping our industrial world.
How digital asset handover is moving from 'data dump' to continuity
A digital twin is a virtual duplicate of a physical entity, like a machine or an entire plant, that uses real-time data from the entity in combination with mathematical models and advanced analytics. In the case of a refinery, it initially gets modeled using static data and design information that is collected upfront, before construction. During the construction phase—and, optionally, during operations and maintenance—the refinery’s virtual duplicate is supplied with data that gives insight into construction or performance. This data is collected dynamically and continually via sensors on site, which gather up-to-date information on parameters relevant to the refinery: temperature, pressure, energy use and more.
The data transfer between an entity and its virtual duplicate often runs in both directions, enabling real-time status updates and offering visibility. Since a digital twin contains data about the past and present of the entity—and since it enables simulations of possible future situations—it lends itself to being used over the course of an entity’s entire life cycle, from design and testing through construction into operations, maintenance and end-of-life processing.
For EPC firms in particular, digital twins hold major promise. They allow decision-makers to virtually test out designs and simulate construction processes without undergoing the risk of experimentation on existing physical systems. They can also evaluate multiple potential scenarios and choose the optimal way forward.
As part of a data-centric approach, sometimes known as EPC 4.0, digital twins enable remote collaboration around a single, updatable version of the truth. Greenfield plants can achieve maximum engineering efficiency while contributing to a digital twin that matures as the project does; brownfield projects can optimize operational assets by trying out different scenarios before undertaking repairs or modifications.
Digital twins also hold promise for EPCs when it comes to asset handover, enabling a richer and more continuous transition of information. According to Keith Tallent, Global Services Manager at KBR, digital twin handover requires careful planning so that the asset always remains up to date. While designing and building an offshore platform for bp in Azerbaijan, KBR first built a digital twin during the engineering phase and later initiated a transition of the digital twin into the operations and maintenance phase. “End users will have the ability to navigate seamlessly between all the information sets in a single, connected environment,” Tallent said at AVEVA World in 2022. “They won’t have to waste time figuring out which system they need to go to in order to access the information they need.”
KBR’s digital twin offering begins with the end in mind, asking at the outset what operations will need to operate the plant. Rob Kennedy, head of Digital Twin at Wood, has similarly advocated for a “right-to-left approach” that reflects operating requirements back into the project phase. “Getting input and getting shared ownership from operations is not optional,” he said. “It is absolutely essential.”
How AI will drive data-centric approaches
Looking forward, the digital twin should position EPCs well to reap the benefits of new industrial technologies as these mature—both those associated with Industry 4.0 and those supporting Industry 5.0.
AI, in particular, can amplify the digital twin’s efficiency and intelligence improvements by enabling more or less autonomous self-optimization on the part of the entity. When paired with a digital twin, AI solutions can accelerate the time to insight while driving predictive maintenance, operations optimization, scenario simulation and efficient asset lifecycle management.
As such, AI looks set to bolster the advantages of having digital assets that draw on data from operations and design phases. For instance, by giving a digital twin an AI chatbot component that has been trained on machines’ maintenance manuals, an operations manager could look at the virtual duplicate of a plant floor and zoom into a machine where something is blinking red. Pulling up a line graph of, say, temperature measurements from a certain part, the manager can then query the AI directly through the twin’s user interface, asking what a likely cause might be—thus leveraging the machine’s manual and the available data—then simulating how possible maintenance solutions might impact other machines on the line.
Already, AI-driven tools for predictive maintenance, predictive analytics and remote monitoring are being mentioned as part of the value offering from EPCs and software providers in the context of data-centric digital approaches. Tallent at KBR, for instance, has said that the firm plans to expand its digital twin offerings into the emerging field of immersive technology by using AVEVA’s Extended Reality (XR) Solutions, which build on AI capabilities.
According to Vaseem Khan, chief engineering officer at McDermott, digital twins involving engineering and process data can provide the building blocks for value-added applications in production optimization, visualization, automation, predictive maintenance—and AI. Khan has described McDermott’s digital twin offering as one that grows in maturity and capability over its lifecycle, from design through construction to operations. “What we are telling our clients is that you need to keep the digital twin alive, either yourself or by using people like ourselves,” he said. "And this digital twin then gets connected to the integrated control system and it starts receiving real-time or near-real-time operating data.”
Ultimately, this integration can open up applications in AR/VR, predictive analytics, advanced process simulations and more. Khan explained that the digital twin continues to learn throughout the life cycle, enabling various AI software tools. “So,” he said, “we create a single integrated facility from conception to end-of-life.”