What is AVEVA Predictive Analytics?
Maximize asset reliability and prevent unplanned downtime with AI-powered predictive maintenance software. AVEVA Predictive Analytics provides time-to-failure forecasting and remedial actions, minimizing repair time and downtime. The no-code environment helps users identify asset anomalies weeks or months before failure occurs.
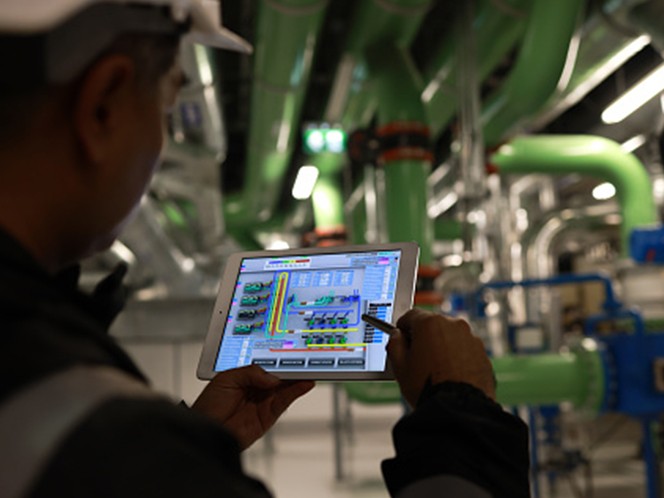
Up to $37 Million CAD
Benefits

Eliminate unplanned downtime
Identify asset anomalies weeks or months before failure

Deploy at scale
Quickly roll out and scale predictive maintenance programs, accelerating time to value

Gain qualitative insights
From analytics to actionable tasks to mitigate failure and capture best practices
Features
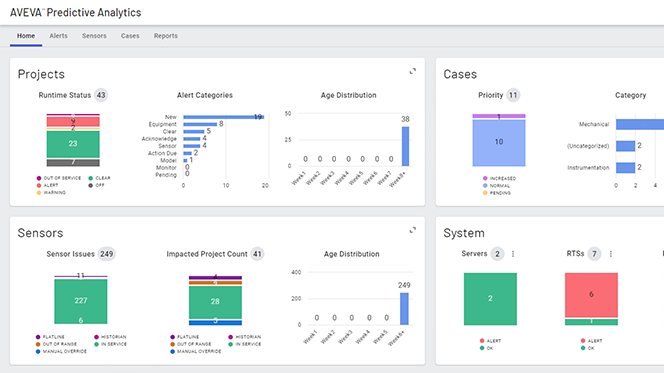
Anomaly detection
Get advanced alerts and utilize case management for knowledge capture and comprehensive reporting. Users without programming or data science knowledge can deploy, validate, and interpret the results of predictive models. Predefined templates accelerate configuration, deployment, and scale-up.
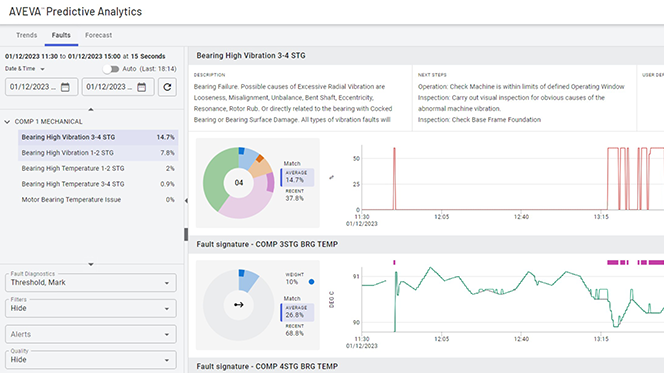
Fault diagnostics
Use customized data and diagnostic tools to gain precise real-time insights, allowing users to perform timely, consistent analysis to quickly diagnose and solve problems. Determine how current performance matches asset fault conditions and identify individual sensors contributing to faults or inconsistencies.
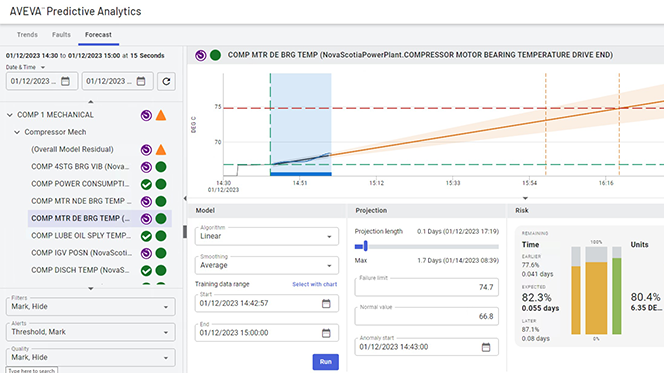
Time to failure forecast
Determine the urgency of repairs with time-to-failure forecasts that provide an estimated time until a failure is likely to occur. Users can plan repair and maintenance strategies that prioritize both safety and profitability, and determine whether to continue operations until scheduled maintenance or initiate an urgent shutdown.
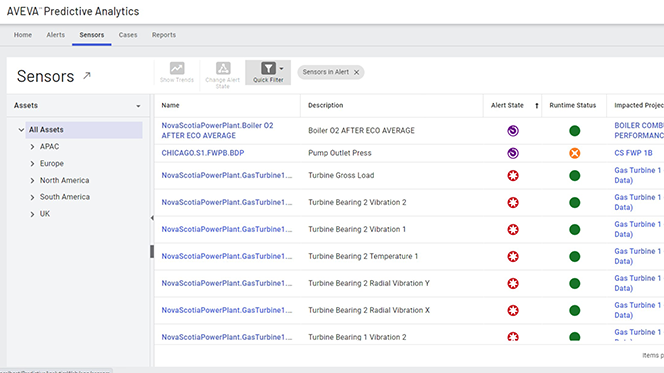
Prescriptive guidance
Use prescriptive guidance and recommended actions from the AVEVA Asset Library, a resource containing more than 22,000 hours of experience, to remediate asset failures. Users can improve decision-making about asset maintenance and performance issues with predefined guidance, minimizing repair time.
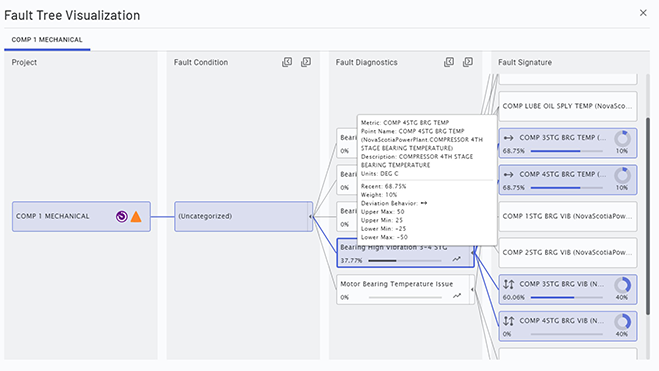
Security
Easily integrate AVEVA Predictive Analytics with existing enterprise security systems. The system supports single sign-on (SSO) authentication and gives administrators detailed user access rights management and editing privileges.
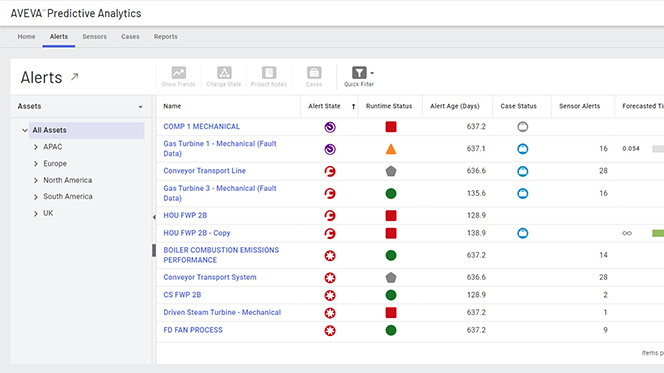
Bring your own algorithm
Include specific algorithms in the predictive maintenance loop using Python or similar language. Monitor all analytics in one application and complement custom algorithms using built-in model templates, data cleansing, alerting, and alert workflow, fault diagnostics, prescriptive actions, forecasting, and case library.
PETRONAS saves millions with early failure detection
PETRONAS, an oil and gas company, used AVEVA Predictive Analytics to notify experts immediately about equipment anomalies. With this cloud-enabled early-warning system, PETRONAS saved $US33 million since implementing in 2019.
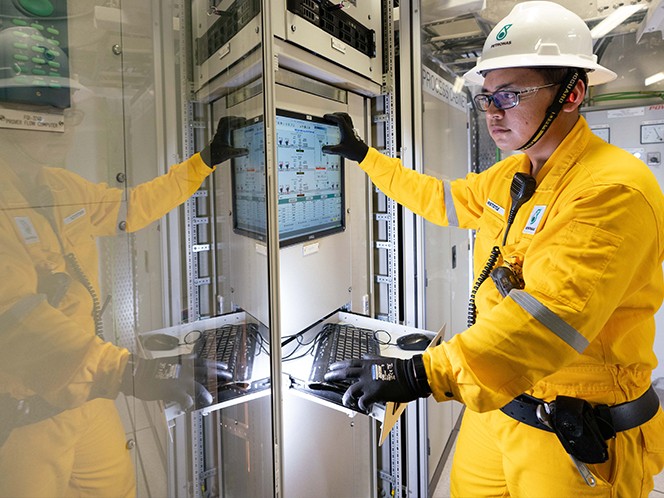
How you can use AVEVA Predictive Analytics
End unplanned downtime
With time-to-failure forecasts, users can plan repair and maintenance strategies in advance and schedule downtime, reducing maintenance costs and minimizing workforce disruption.
Improve sustainability
Predict and prevent failure by detecting anomalies before they occur with accurate asset health information, reducing resource use and energy consumption.
Maximize reliability and performance
Identify equipment problems before they turn into productivity loss and asset failures. Monitor asset performance continually in real time and get instant alerts when an asset starts to deviate from normal operations.