Fundamentally transform how industry works
Digital transformation drives value through shared industrial information and insights. When you have easy access to aggregated, curated and shared information from your sites and assets, collaboration no longer requires a visit -- or even an email. Reliable information is instantaneous, available to every member of your team wherever they are, improving hand-offs, maximizing efficiency and minimizing errors.
Moreover, AI software finds patterns in your industrial information beyond the scope of what people can spot on their own, identifying opportunities and failures that may have otherwise been missed.
And with visualizations that leverage AR/VR, you and your team can grasp the significance of the information more quickly and holistically, giving you the confidence to make fast, accurate decisions.
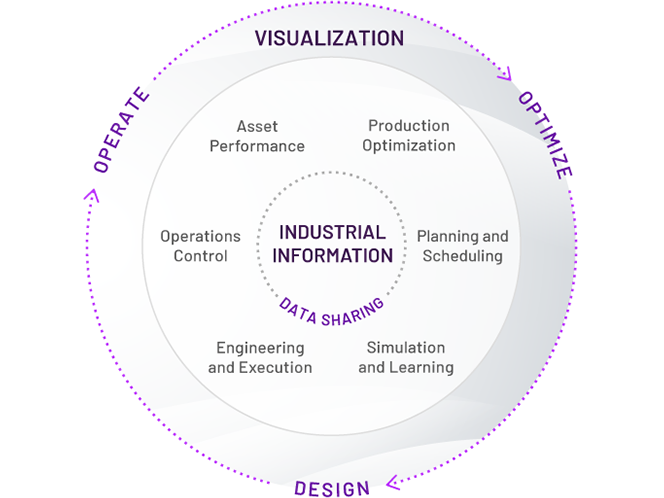
How digital transformation benefits your business
Accelerate innovation and learning
Bring agility to the entire process and plant lifecycle of design, simulation, training, and operations.
Empower your workforce to increase efficiency
Integrate your workforce and gain valuable insights that help you streamline operations.
Gain visibility across the industrial cycle
Share data within—and beyond—the organization to promote collaboration and harness new business opportunities, align teams, and promote collaboration.
"AVEVA created the first digital transformation solutions for industry that span the entire lifecycle—from conceptual engineering through operations and supply chain."
LNS Research
Aker Carbon Capture increases operational efficiency by 50%
Aker used AVEVA Unified Engineering to create replicable designs for carbon capture units, maximizing efficiency by collaborating across time zones.
Henkel boosts efficiency, saves €8 million in six years
Henkel, a global leader in consumer goods and industrial chemicals deployed a digital backbone using AVEVA, meeting their sustainability and OEE solutions goals.
Continue your digital transformation journey
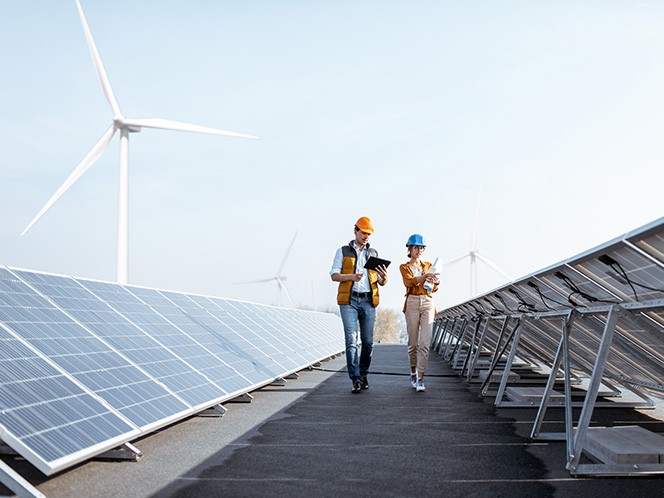