Value Chain Optimization overview
Make better decisions faster across your operations life cycle. End-to-end value chain optimization helps you to redefine your processes to enable deeper collaboration, reduce value leaks and sustain productivity and innovation.
Value Chain Optimization features
React faster than the rapidly changing market. Achieve your sustainability goals using innovative technologies.
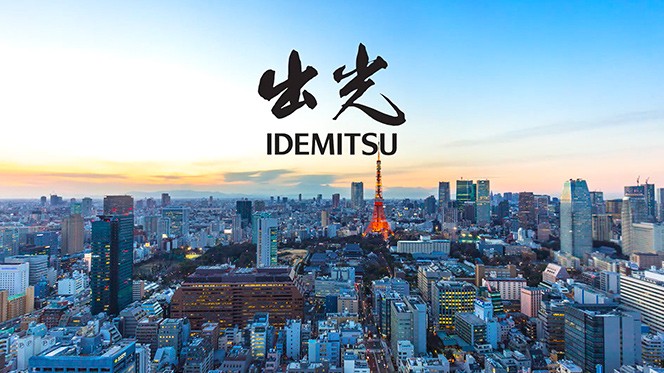
Idemitsu Kosan transforms its refining operations with AVEVA Value Chain Optimization
A volatile O&G industry required Idemitsu Kosan to adopt AVEVA Value Chain Optimization for decision-making across seven refineries, improving refinery margins and business processes.
Value Chain Optimization products for continuous process industries
AVEVA Unified Supply Chain
Formerly Known As Spiral Unified Supply Chain Management
Optimize YOUR Supply Chain with the ultimate cloud-enabled oil and gas supply chain management software from AVEVA. Faster, smarter, and tailored for O&G.
AVEVA Process Optimization
Formerly Known As ROMeo Process Optimization
Boost Profitability with Real-Time Process Optimization by maximizing your operating profit and improving plant performance with AVEVA Process Optimization.
AVEVA Off-sites Management
Formerly Known As Refinery Off-Sites
AVEVA Offsites Management provides accurate, reliable, and accessible inventory and movement information, movement automation and more!
AVEVA Production Accounting | Yield Accounting
Formerly Known As ErrorSolver
Transform your oil and gas production accounting. Streamline your operations and increase productivity with AVEVA's powerful production accounting software.
Advanced Process Control | AVEVA APC
Formerly Known As Advanced Process Control
Improve your oil and gas operations with AVEVA APC. Our model predictive control technology extracts maximum value from your processes.
AVEVA Process Optimization: Reactor Models
Rigorous kinetic models integrated with Reactor Models provide optimization, LP update, performance monitoring, as well as offline simulation.
Value Chain Optimization products for manufacturing
AVEVA Manufacturing Execution System
Formerly Known As Wonderware MES
Maximize profitability, flexibility, quality, and compliance in manufacturing by digitally managing the rules and information for all operational activities and plant events in real-time. A work process-centric and Model-driven approach reduce the time to value and cost of ownership for both plant deployments and multi-site MES rollouts.
AVEVA Recipe Management
AVEVA Recipe Management reduces recipe management efforts and automates formula download and recipe execution on automated equipment. Streamline the new product introduction process and increase manufacturing flexibility while securing process and product quality.
AVEVA Batch Management
The control system independent batch management software provides guidance and oversight to both recipe management and batch execution with a complete history record (EBR). Effectively manage and automate large, multi-product and multi-stream batch operations to maximize plant throughput, increase manufacturing flexibility and to deliver consistent quality to recipe specification.
AVEVA™ Insight
AVEVA Insight delivers actionable information and Artificial Intelligence capabilities to help your teams improve asset reliability and operational performance.
Advanced Process Control | AVEVA APC
Formerly Known As Advanced Process Control
Improve your oil and gas operations with AVEVA APC. Our model predictive control technology extracts maximum value from your processes.