Data-led manufacturing for supply chain resilience
Posted: July 08, 2025
In an era where unpredictability is the only constant, the resilience of a manufacturing company’s value chain has never been more critical. Geopolitical conflicts and pandemics have upended manufacturing schedules, blocked transportation routes, and destabilized global labor markets. Extreme weather events, from wildfires to floods, have disrupted production and transport. On top of that, rising inflation and tariffs have increased the cost and complexity of sourcing raw materials.
According to McKinsey research, companies across industries experience major supply chain disruptions—disruptions that last a month or longer—every 3.7 years.[1] And these disruptions cost companies a significant amount of time and money. In the consumer goods sector, the cost of these disruptions over a decade is equal to about 30% of a company’s annual earnings before interest, taxes, depreciation, and amortization (EBITDA).[1]
But manufacturing companies can shift their supply chain strategies toward a more proactive approach. By having systems in place that allow them to act quickly when disruptions occur, companies can transform these supply chain challenges into opportunities for innovation and growth.
Understanding supply chain vulnerabilities
Traditional manufacturing strategies focus on maximizing efficiency, making the product at the lowest cost. This strategy often means insulating the plant from external disruptions. However, as AVEVA’s Sree Hameed writes, “Insulating the plant from volatility also insulates it from corporate. Anyone outside of the plant views it as a black box. This lack of visibility makes it difficult to engage the plant in modernizing the supply chain strategy to achieve greater agility and resilience.”[2] So how do manufacturing companies open up that black box?
As McKinsey researchers emphasize, the first step for companies to build resilience is to understand supply chain vulnerabilities: “Which suppliers, processes, or facilities present potential single points of failure in the supply chain? Which critical inputs are at risk from shortages or price volatility?” Of course, it is impossible to imagine every possible scenario that threatens a company’s value chain—who could have predicted the extent of the supply chain disruptions caused by COVID-19?—but understanding where a company’s vulnerabilities lie is crucial to remaining agile when the unexpected occurs.
Part of preparing for the unexpected involves rethinking how data, people, and processes interact across the enterprise. Digital tools that offer companies operational transparency, connected workers, advanced planning, and performance monitoring can allow manufacturers to proactively address supply chain disruptions.
Visibility and operational transparency
A resilient value chain starts with visibility. Companies must be able to see across their operations in real time to make informed decisions quickly.
Kellogg’s: Remaining agile with contextualized plant-floor data
Kellogg’s, a household name in the food and beverage sector, needed better visibility into its operations to reduce waste and energy use. Siloed production data and reliance on manual analysis made it hard to identify inefficiencies and respond quickly. So Kellogg’s implemented a real-time data infrastructure with contextualized plant-floor data.
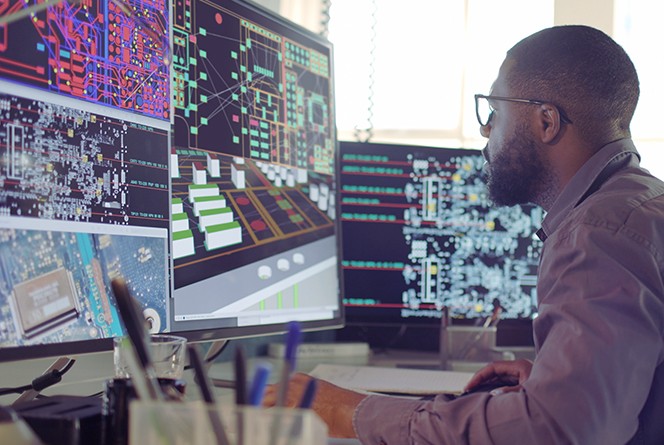
This system captures information on production rates, changeover speeds, losses, and inventory levels, automatically pulling reason codes from equipment PLCs for downtime alarms. Just one initiative saved the company $3 million per year in energy usage. With a comprehensive view of end-to-end operations and asset health, teams can identify bottlenecks and discover new ways to optimize asset performance and production processes—which help them overcome supply-chain challenges and other unexpected disruptions to operations.
Closing the knowledge gap with data-driven decision-making
A resilient, agile supply chain strategy requires a skilled, flexible workforce. As experienced workers retire and institutional knowledge walks out the door, manufacturers are increasingly turning to digital tools to preserve expertise and empower the next generation of operators. By making sure workers have access to the right information at the right time, organizations can remain agile when challenges arise.
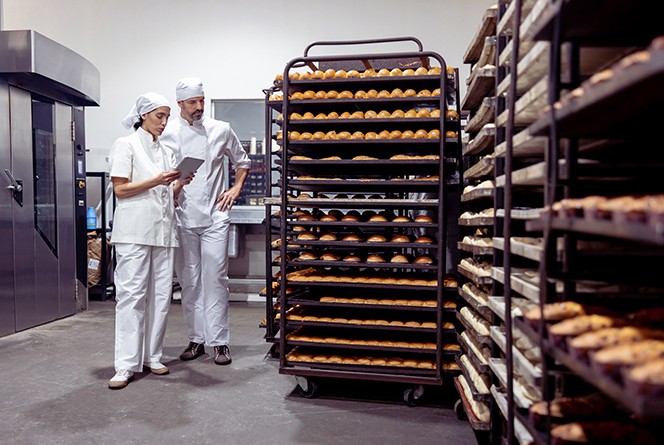
Leclerc: Bridging experience gaps with a connected worker platform
Leclerc, a leading snack food manufacturer for more than 110 years, was losing workers to retirement, losing the institutional knowledge vital for best practices across its three factories. So it deployed a connected worker platform to standardize training using that institutional knowledge, ensuring that critical operational knowledge is easily accessible on the plant floor.
Leclerc saw significant improvements in organizational learning after the implementation of this platform and a reduction in unplanned downtime across its facilities. This human-centric resilience bolsters the supply chain by ensuring production can continue smoothly despite workforce turnover.
Improving manufacturing quality with digital traceability
In industries like food and beverage or pharmaceuticals, quality is non-negotiable. Manufacturers need digital traceability to ensure compliance, maintain standards, and respond swiftly to quality issues.
F&N Dairies: Achieving 100% first-time quality at scale
F&N Dairies produces three million cans of milk per day. Quality is critical to maintaining consumer trust, but tracking parameter deviations was a manual process for operators, error-prone and inefficient. Using a mix of a data historian, batch management tools, and an MES solution, F&N Dairies improved its tracking and traceability with a digital solution.
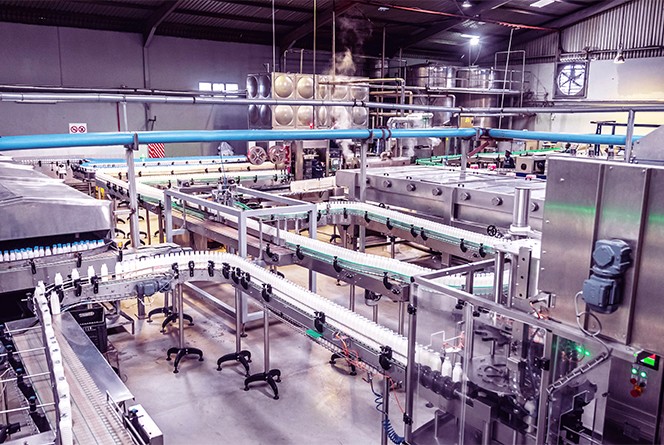
The solution enabled the dairy to reach its production goal of 2,500 cans per minute, reduced quality traceability report time from four hours to one minute, and helped the plant achieve 100% first-time quality, which means products are manufactured correctly the first time without inspection, rework, or replacement. F&N Dairies also used batch management software to manage batch operations, perform recipe modeling, and develop batch execution automation. This means plant operators can quickly deploy and run revised or new product recipes without control system changes, reducing time to market and allowing the dairy to remain agile when the unexpected occurs.
Smarter production scheduling
Supply-chain volatility also disrupts manufacturing schedules. Late material deliveries, sudden demand spikes, or capacity constraints require agile, intelligent digital planning tools.
Graphic Packaging International: Planning ahead with data
Graphic Packaging International’s plants relied on tribal knowledge for scheduling. This made it difficult to commit to customer orders and adapt to demand changes. With the implementation of advanced planning and scheduling tools, the company digitized and optimized production schedules, providing real-time changeover visibility, constraint-based scheduling, and data-driven decision support.
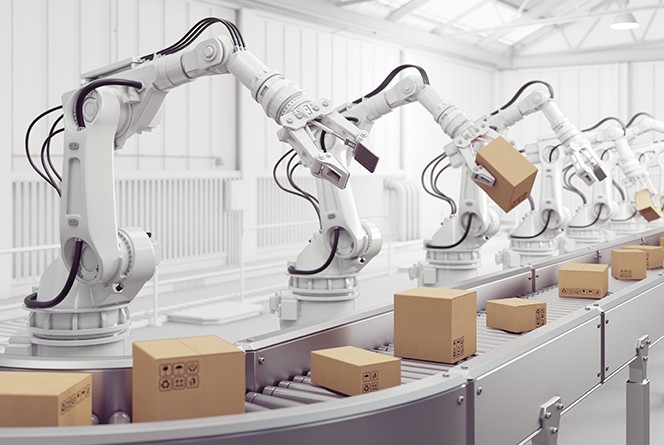
This improved scheduling enabled the company to meet its capacity goals and reduce scheduling errors. Better run sequencing also drove higher equipment utilization (OEE), which cut unit production costs by 6%, translating to about $16 million in annual savings. By basing production plans on live data rather than intuition, the company increased its supply reliability for customers—a direct boost to supply chain resilience and efficiency.
Turning disruption into opportunity
As volatility becomes a permanent feature of the manufacturing landscape, value-chain resilience is no longer a luxury—it’s a necessity. Companies that invest in visibility, agility, and traceability will be better positioned to navigate disruptions and capitalize on new opportunities.
Through real-time data integration, collaborative tools, and standardized platforms, manufacturers can build a more connected, intelligent value chain. One that’s not only prepared for the next disruption—but ready to lead through it.
[1] Henrich, J., Li, J., Mazuera, C., & Perez, F. (2022, June 14). Future-proofing the supply chain. McKinsey & Company. https://www.mckinsey.com/capabilities/operations/our-insights/future-proofing-the-supply-chain
[2] Hameed, Sree. (2023). Enabling agility through digital manufacturing in the post-pandemic era. AVEVA. https://www.aveva.com/content/dam/aveva/documents/white-papers/WhitePaper_AVEVA_EnablingAgility_ConsumerProducts_23-05.pdf
Related blog posts
Stay in the know: Keep up to date on the latest happenings around the industry.