Do more with AVEVA engineering software
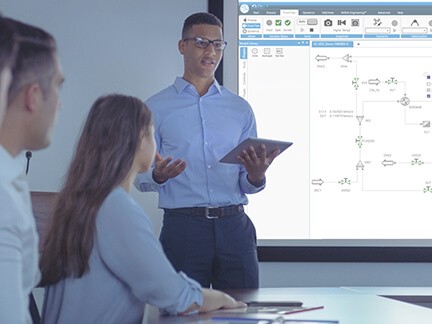
Simulation and learning
Accelerate process design and reduce operational risk.
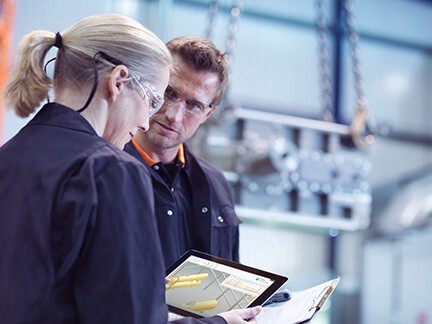
Engineering and execution
Maximize engineering efficiency in capital projects and operations.

Engineering data management
Ensure your teams have reliable, relevant, and timely information.
“AVEVA’s cloud-based and data-centric engineering enables our teams all around the world to work remotely, yet together, on one platform that spans all of our engineering data.”
Thomas Cheylan, Projects Performance Director, Veolia Water Technologies
Aker Carbon Capture increases efficiency by 50%
Aker used AVEVA Unified Engineering to create replicable designs for carbon capture units, maximizing efficiency by collaborating across time zones.
Featured engineering products
AVEVA™ E3D Design
Formerly Known As AVEVA Everything 3D
AVEVA E3D Design is a 3D design software used in process plant, marine and power industries. It helps create designs and drawings and reduce costs and project risks.
AVEVA™ Unified Engineering
AVEVA Unified Engineering is a data-centric engineering environment. Engineer and collaborate across all project phases and multi-discipline teams in real time.
AVEVA Process Simulation
Formerly Known As SimCentral Simulation Platform
Design sustainable processes, products, and plants at the speed the market demands. AVEVA Process Simulation moves beyond linear, wasteful workflows to enable a circular, sustainable world.
AVEVA™ Asset Information Management
Accelerate information discovery and break down silos for fast, intuitive, in-context access to relevant data.
AVEVA PRO/II Simulation – The Trusted Steady-State Process Simulator
Formerly Known As PRO/II Process Engineering
A simulator that optimizes plant performance improves your process design and operational analysis by performing engineering studies.
AVEVA Unified Learning
Formerly Known As Enterprise Wide Learning
Experiential learning to build and sustain competence for today’s industrial workforce. Eliminate operator error and ensure consistent performance.