Optimizing Power-to-X processes with AVEVATM Process Simulation
Posted : 10 June 2025
The global shift toward renewable energy has accelerated the development of Power-to-X (PtX) technologies, which convert surplus renewable power into valuable products such as hydrogen, synthetic fuels, and chemicals such as ammonia and methanol. To ensure the economic feasibility and efficiency of these processes, engineers need powerful simulation tools that enable detailed process modeling, optimization, and performance evaluation. AVEVA Process Simulation provides a comprehensive platform for designing and optimizing PtX processes, allowing engineers to make informed decisions and maximize efficiency.
Challenges in PtX optimization
While PtX processes present promising solutions for decarbonization, several challenges must be addressed:
- Efficiency: Energy conversion and utilization must be maximized to reduce losses.
- Economic feasibility: High capital and operational costs can be barriers to large-scale adoption. Expensive electrolyzer technology or battery storage may be needed to keep the PtX plant at minimum turndown rather than shutting down or importing power. Because this equipment can be very expensive, design optimization is crucial.
- Variability of renewable power: Changing solar and wind-based power means that the process may never be steady and dynamic simulation is required.
- Scalability: PtX processes need to be optimized for different production scales and applications.
The role of process simulation in PtX
AVEVA Process Simulation provides an advanced platform for modeling, analyzing, and optimizing PtX processes during conceptual and pre-feed engineering. Its main benefits are:
1. Accurate process modeling
Developing an efficient PtX process starts with a thorough feasibility study. AVEVA Process Simulation helps engineers evaluate feedstock requirements and energy balances and Identify process bottlenecks and potential inefficiencies.
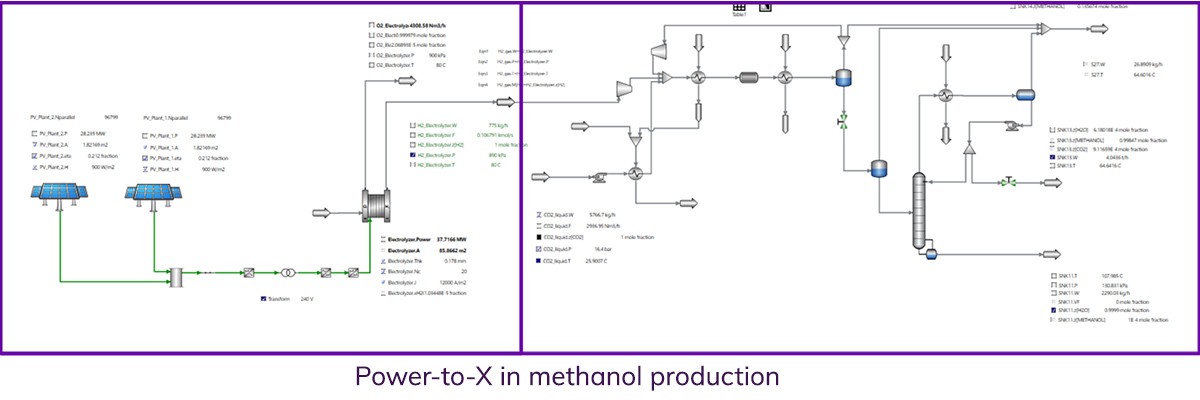
2. Dynamic simulation for feasibility and economic analysis
One of the biggest challenges in PtX is designing a plant for variable renewable power. AVEVA Process Simulation enables users to enter a year of weather data to understand how the plant will behave and:
- Understand if power must be imported and negotiate a power purchase agreement (PPA).
- Minimize battery or hydrogen storage to survive weather-related shortages of renewable power.
- Evaluate different electrolyzer technologies (e.g., PEM, alkaline, SOEC) to understand how repetitive startups and shutdowns will degrade behavior over a year of operation.
3. Cost and economic analysis
PtX processes require significant capital investment, making economic evaluation a crucial step. AVEVA Process Simulation allows for:
- Techno-economic assessments by integrating cost models with process models.
- Adding CapEx and OpEx costs for renewables, electrolytes, and calculating the Levelized Cost of Hydrogen (LCOH) or Levelized Cost of Product (LCOP) for ammonia or methanol, as these are not stable due to variable operations because of variations in renewables.
4. Dynamic simulation for process control
Dynamic modeling in AVEVA Process Simulation is critical for understanding transient behavior and designing effective control strategies. This is especially important in PtX systems, where energy input from renewable sources can be highly variable. Benefits include:
- Designing robust control loops and automation strategies.
- Identifying process bottlenecks and potential inefficiencies.
- Predicting system behavior under different load conditions.
- Evaluating startup, shutdown, and emergency response scenarios.
5. Sustainability and carbon footprint reduction
With growing emphasis on carbon neutrality, PtX must be designed to minimize environmental impact. AVEVA Process Simulation supports sustainability analysis by:
- Calculating carbon emissions and energy consumption.
- Evaluating different carbon capture and utilization (CCU) strategies.
- Assessing green hydrogen and synthetic fuel production pathways to ensure compliance with environmental regulations.
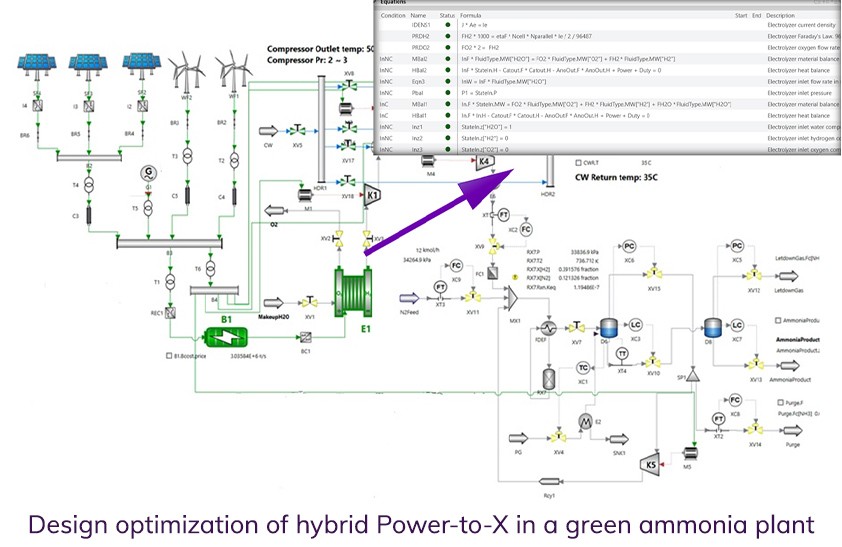
Case study: Leading Canadian hydrogen and green ammonia producer
A leading Canadian hydrogen and ammonia producer used AVEVA Process Simulation to design a techno-economic simulation model for a 650MW Green H2 facility.
Intermittent renewable power and a complex PPA made it difficult for them to estimate H2/NH3 production by using basic tools. In addition, unknowns from the conceptual engineering phase could dramatically increase the LCOH and LCOA.
By using AVEVA Process Simulation, they managed to:
- Provide early insight into production performance and costs (LCOH, LCOA).
- Assist in PPA negotiations, intermediate storage decisions, and equipment sizing.
- Define the optimal operating point for the integrated plant.
- Run case studies quickly and refine the model as new data becomes available.
Ready to find out more about how you can model green hydrogen processes with AVEVA Process Simulation?
Related blog posts
Stay in the know: Keep up to date on the latest happenings around the industry.