Smarter chemicals: AI applications in the chemicals sector
Posted: July 08, 2025
To stay competitive amid rising material costs and market volatility, chemical companies face a challenge familiar across heavy industries: they must do more without using more. That means delivering higher yields without consuming more materials; achieving greater throughput without using more energy; and boosting productivity without increasing their carbon footprint. The only way to produce more output without more input is by operating at much higher levels of efficiency. This is where industrial AI is poised to make all the difference.
While many heavy industries are embracing AI headlong, the chemical industry has remained comparatively slow in its adoption. According to a recent IBM report, while 80% of chemicals company executives said AI will be important to their businesses in the immediate years ahead, only four in ten chemicals companies have executed enterprise-wide AI strategies.[1] And, according to a recent McKinsey Global Institute survey, the chemicals industry has the lowest exposure to gen AI tools as well—just 14% compared to the 23% cross-industry average.[2]
There are a number of reasons for this. Innovation cycles are long; regulatory demands are stringent; upfront investments are dissuasive; and because the industry is largely B2B, customer bases are less diverse and more concentrated, reducing the urgency for scalable, customer-facing AI solutions and limiting the data-driven feedback that often spurs more rapid AI development in other sectors.[3] But that’s all starting to change.
What are the leading applications of AI in chemicals industry?
Today, pioneering chemicals companies are showing their industry peers that AI is more than a useful tool; it is an essential tool. Their success stories cluster around a few high-impact use cases:
- Process optimization
- Predictive analytics
- Hybrid simulation
- Material discovery
Let’s take a look at how AI can help chemicals companies build more profitable businesses and a more sustainable future.
AI-driven process optimization
Chemical plants generate massive volumes of sensor data—temperatures and pressure, flow rates and composition and so on—which makes chemical processes incredibly complex. Optimizing those processes is even more complicated; it requires chemical companies to identify often subtle, easy-to-miss patterns hidden in this sea of high-dimensional data.
While the size and complexity of the task may strain human process engineers and traditional tools beyond their limits, AI is perfectly suited to digesting and analyzing datasets at this gargantuan scale. By continuously monitoring and learning from historical and real-time process data, AI can make recommendations to adjust control parameters to improve yield, throughput, energy efficiency, and quality consistency.
Chemical companies are already seeing striking successes with AI-driven process optimization. The International Group Inc. (IGI), a wax producer, partnered with Lityx and AVEVA to drive process optimization across its nine US-based plants. Together, they developed an advanced, AI-powered solution capable of analyzing thousands of data points at once to identify where a process is losing efficiency, where it’s working well, and where to find opportunities for improvement.
The project resulted in a remarkable 67x ROI. In just one year, higher yields generated $10M in profit. The new system also helped IGI reduce crude waste by 49% and eliminate 20 hours of off-spec processing every two weeks.
AI-infused predictive analytics and maintenance
One of the earliest and most widespread use cases for AI in chemicals operations is predictive analytics and maintenance. Machine-learning algorithms analyze historical and real-time data, detect patterns, and forecast future equipment failures or performance issues weeks or even months in advance. By learning from data over time, these models give plant operators the time, foresight, and guidance they need to address issues before they become big problems, minimizing downtime and improving reliability.
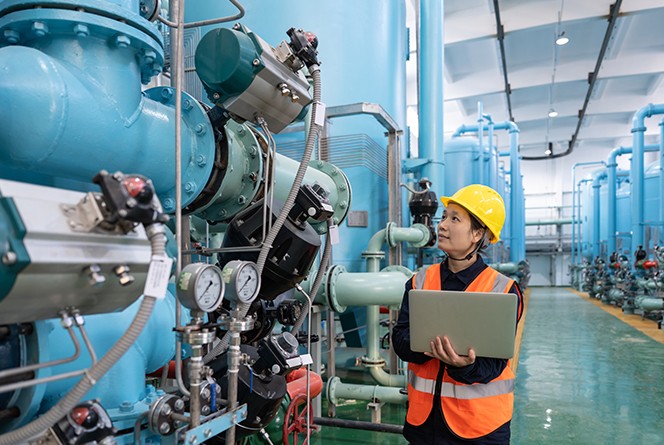
In the chemicals industry, as in other heavy industries, more reliable operations can quickly add up to dramatic OpEx savings. Thailand’s largest petrochemical company, SCG Chemicals, proves the point with its new Digital Reliability Platform. SCG’s platform combines AI-infused predictive analytics and advanced asset performance management software into a cutting-edge operations digital twin that continuously monitors critical assets in real time, detects anomalies, and delivers prescriptive maintenance recommendations.
The AI-infused platform helped SCG boost plant reliability to 99%, significantly enhanced operational efficiency, and led to a ninefold return on investment in just six months.
AI-augmented simulation
Traditional process simulation models are built on first principles—rigorous thermodynamic or physics equations that fully define processes within a given piece of equipment. These mechanistic, equation-based models are incredibly accurate when you have all the required input data. However, if you lack input data, like kinetic parameters or the thermodynamic properties of a particular fluid, model accuracy suffers, particularly in complex reactions.
Machine-learning simulation models can address these limitations. By training on historical and real-time operating data, machine-learning models can rapidly generate accurate reaction predictions even when all underlying mechanisms aren’t fully understood. And when we combine equation-based models with machine-learning models, the result is hybrid modeling, the best of both worlds: The transparency and rigor of first-principles models with all the flexibility and predictive power of AI.
It is still early days for hybrid modeling, but pioneering chemicals companies are already demonstrating its value. Take Isu Chemicals, for example. The company used six years of reactor data to build a hybrid model that could predict reactor yield with 99.7% accuracy. That gives engineers the insight they need to now optimize reactor conditions with greater confidence, reduce trial-and-error experiments, and improve output without compromising safety or quality.
By combining historical operating data with first-principles simulation, hybrid modeling helps fill in knowledge gaps while still retaining the engineering logic behind the process. This results in smarter simulations, faster decision-making, and ultimately, more efficient, cost-effective production.
AI-powered material discovery
Beyond optimizing what happens inside the reactor, AI is beginning to accelerate the discovery and design of what goes into it. Using traditional, trial-and-error strategies, discovering new molecules and materials is expensive and slow. The lead time between molecule discovery and commercialization can take up to twenty years.[4] AI-powered material discovery is poised to dramatically compress the R&D cycle.
By combining deep learning and physics-based simulation with generative AI, advanced AI models can generate the designs of thousands of new molecules and materials and predict their stability—not in years, but hours. Recently, Google DeepMind’s new deep learning tool, Graph Networks for Materials Exploration (GNoME), discovered 2.2 million new inorganic crystals, more than 700 of which have already been independently created in labs around the world.[5] Inorganic crystals are essential to a wide variety of modern technologies, like computer chips, solar panels, and batteries.
AI-accelerated material is great news for many—researchers, consumers, for the healthcare and biomedical fields, but it’s especially great news for the environment. AI models can help identify non-toxic alternatives to harmful industrial chemicals, new biodegradable alternatives to traditional plastic, eco-friendly construction materials, and new materials for batteries and other critical renewable energy technologies.
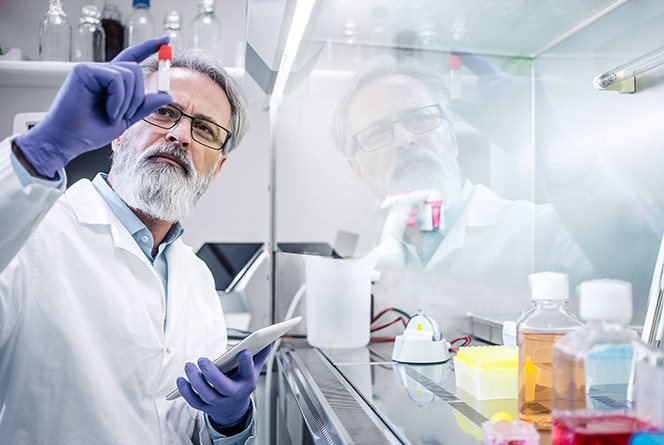
Recently, Microsoft and the Pacific Northwest National Laboratory partnered to find new materials to replace or reduce the lithium (which is relatively scarce and expensive) needed for EV batteries. The team is testing a combination of sodium and lithium that could reduce the lithium content in batteries by as much as 70%.[6]
How will AI continue to shape the chemicals industry?
AI today is already helping to create more efficient, reliable chemical operations. In the years ahead, we’re sure to see even deeper, broader transformations—from novel AI-generated chemical compounds all the way to autonomous self-driving labs. As AI matures, and adoption accelerates, AI won’t just optimize chemical production; it will open new frontiers in innovation, sustainability, and competitive advantage.
[1] IBM Institute for Business Value. (2020, September 30). Optimizing the chemicals value chain with AI. IBM. https://www.ibm.com/thought-leadership/institute-business-value/en-us/report/chemicals-value-chain-ai
[2] Chui, M., Hazan, E., & Lal, A. (2022, October 26). How AI enables new possibilities in chemicals. McKinsey & Company. https://www.mckinsey.com/industries/chemicals/our-insights/how-ai-enables-new-possibilities-in-chemicals
[3] Ibid.
[4] Cole, J. M. (2020). A thermoelectric materials database auto-generated from first principles. Accounts of Chemical Research, 53(3), 599–610. https://doi.org/10.1021/acs.accounts.9b00470
[5] DeepMind. (2023, December). Millions of new materials discovered with deep learning. DeepMind Discover. https://deepmind.google/discover/blog/millions-of-new-materials-discovered-with-deep-learning/
[6] Microsoft. (2024, June 6). How AI and HPC are speeding up scientific discovery. Microsoft Source. https://news.microsoft.com/source/features/sustainability/how-ai-and-hpc-are-speeding-up-scientific-discovery/
Related blog posts
Stay in the know: Keep up to date on the latest happenings around the industry.