As the world grapples with climate change, green hydrogen is emerging as a viable solution for clean heating, electricity, and fuel. Protium, the U.K.’s largest green hydrogen developer, is working to generate and transport green hydrogen to help industrial customers reach their 2030 CO2 abatement goals. But delivering cost-effective hydrogen requires building new physical infrastructure and facilities—and ensuring efficient operations requires the right set of digital tools to provide critical visibility and insights. Using an integrated set of AVEVA solutions, Protium implemented data collection, analysis, and simulation solutions, including digital twins, to optimize operations, maximize its equipment network, and drive innovation in the green hydrogen industry.
Challenges
Emerging industry needs flexible digital infrastructure to cost-effectively manage a network of innovative physical infrastructure
Monitoring and optimizing a large and diverse network of physical assets
Lack of established operations, procedures, and methods for deploying new digital tools, technology, and processes
Results
295%
projected return on project investment
5-10%
additional reduction in CO2 emissions compared to goals

Optimized hydrogen venting, reduced water and electricity use, and minimized material waste
15%
increase in reliability
30%
reduction in staff time using process simulation
15%
reduction in maintenance spend
Solutions
Protium used AVEVA™ Process Simulation and is in the process of deploying AVEVA™ PI Vision™, AVEVA™ PI Server, and AVEVA™ System Platform to collect, contextualize, analyze, and visualize asset performance and operations data. This includes deploying a digital twin to optimize its end-to-end green hydrogen production, compression, and logistics network.
Building a connected hydrogen pipeline
Protium’s green hydrogen production facilities use electrolysis to split water molecules into hydrogen and oxygen using renewable electricity. Once generated, pure hydrogen is compressed for storage and either used locally or transported via tube trailer.
To help customers on their journey to net zero with less upfront investment and less risk, Protium delivers hydrogen as a service under contracts, similar to traditional utilities like electricity and water. To achieve profitability, Protium is vertically integrating by generating its own renewable electricity resources to manage costs, owning required infrastructure such as compressors and storage, and establishing logistics networks across the U.K. and Europe.
Protium’s innovative infrastructure includes Pioneer 1, the company’s containerized, fully automated electrolyzer solution, and Pioneer 2, the company’s second-generation hydrogen production facility, projected to deliver 25 times more (900 kilograms) hydrogen every day.
While Protium has made incredible strides in bringing green hydrogen to market—its current pipeline is projected to produce over 500 MW of renewable resources—doing it efficiently and profitably is not without hurdles. The digital team has had to build an entirely new digital infrastructure to support the innovative new physical infrastructure. Availability, reliability, and scarcity of renewable energy are always challenges. So, with the goal of efficiently supporting future growth, the team decided to use AVEVA’s connected, hybrid software solutions.
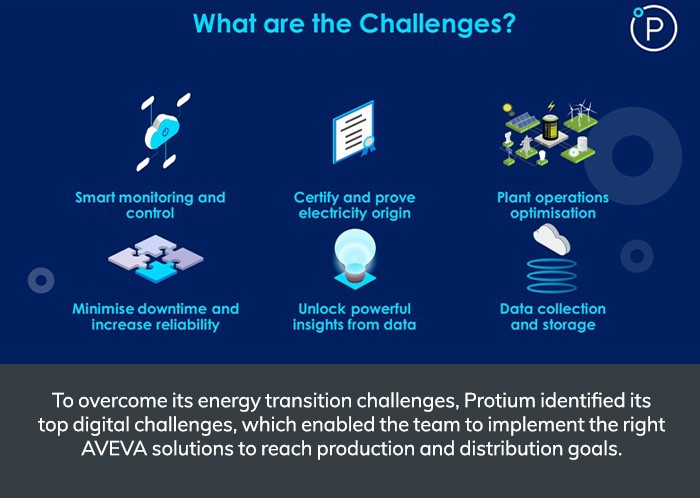
“We believe that digital will enable us to deliver green hydrogen to people on a cost-effective basis in the future.”
-- Jon Constable ,COO, Protium
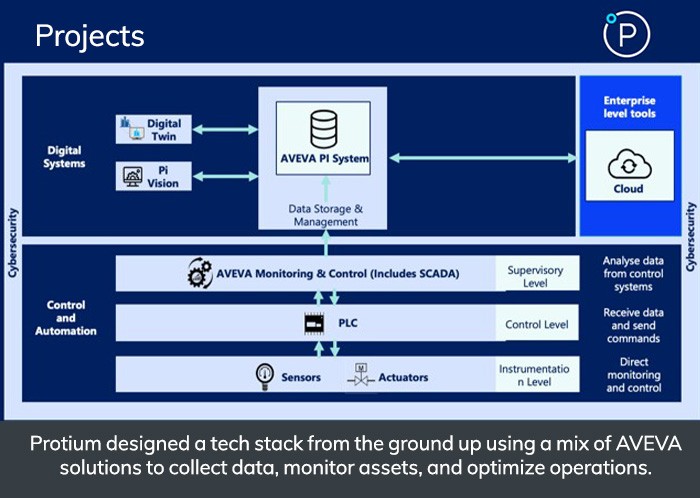
AVEVA solutions net a 295% return on investment
When Protium built its digital strategy and corresponding tech stack, it was important to create a flexible design that would work across all stages of a project, including feasibility studies, operations, engineering, and design. To get there, Protium will deploy AVEVA solutions to collect data from Pioneer 2 using telemetry, sensors, and PLCs, and push that data to AVEVA™ System Platform so engineers will be able to monitor operations in real time.
Data collected from on-site sensors will be fed into AVEVA™ PI System™, where users can visualize contextualized data in dashboards and perform real-time analytics. The AVEVA PI System also interfaces with the enterprise SCADA environment so users can optimize day-to-day operations. Using AVEVA™ Process Simulation, users have built real-time digital twins to detect faults and perform error analysis. Protium also makes data and insights available in the cloud for all stakeholders, allowing users to integrate operations data into the CMS and ERP systems for planning maintenance, financials, and projects.
Thanks to AVEVA solutions, users can plan current and future infrastructure, build digital twins to optimize systems, and set up real-time alerts and KPIs to minimize downtime. Overall, AVEVA solutions have enabled Protium to reduce staff time by 30%, increase reliability by 15%, reduce maintenance spend by 15%, and more—and are projected to generate an overall rate of return of 295%.
“The AVEVA PI System and AVEVA System Platform, together with the real-time digital twin, will truly make us have transparency and control of the assets and production plans.”
—Pietro Beretta Data Scientist, Protium
A digital twin lays the groundwork for future benefits
A critical part of Protium’s project success is the digital twin of Pioneer 2. AVEVA Process Simulation lets the team use drag-and-drop items from its model library in advance of validating and optimizing the twin. The digital twin connects to AVEVA™ PI Server so users can directly and easily import data. In just a short time, the digital twin has benefitted users across the organization. The team can easily check engineering calculations, which reduces outsourcing, as well as better manage and plan downtime with customers, and even improve productivity by better modeling projects in advance.
Next, the Protium team plans to perform additional simulations and operationalize its Pioneer 2 electrolyzer. Overall, Pioneer 2 is expected to save 256,000 tons of CO2 per year, but the team is projecting that AVEVA solutions will help them save an additional 5-10% by optimizing process design, reducing utility consumption, and more.
“I don’t have any simulation experience. This was my first time using simulation software, but from my experience, it was incredibly easy to use, the user interface was very clear, it’s very easy to connect different models together and build up the process as you go on.”
—Cameron Rout, Technical Engineering Associate, Protium
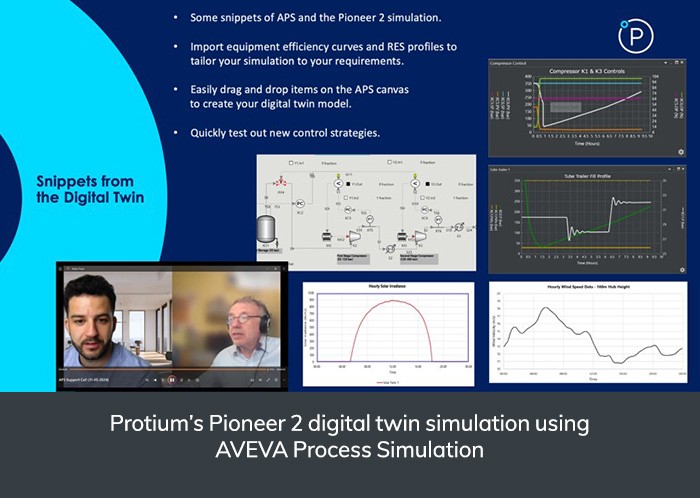
Product highlights
AVEVA™ PI System™
Collect, aggregate, and enrich real-time operations data for immediate problem-solving and easily deliver formatted data to enterprise applications and advanced analytics.
AVEVA PI Vision
With AVEVA PI Vision, turn raw data into rich, visual displays and share valuable insights across your enterprise.
AVEVA PI Server
Learn about the trusted, high-volume, and real-time data storage, contextualization, analytics, and notification engine at the heart of AVEVA™ PI System™.
AVEVA System Platform, formerly Wonderware
Contextualize operations with responsive, standards-driven, and scalable software for deploying advanced SCADA, MES, and IIoT. Unify people, processes, and assets.
AVEVA Process Simulation
Formerly Known As SimCentral Simulation Platform
Design sustainable processes, products, and plants at the speed the market demands. AVEVA Process Simulation moves beyond linear, wasteful workflows to enable a circular, sustainable world.