Enabling the Digital Twin through Unified Engineering
Posted: June 10, 2023
For decades, most Engineering, Procurement, and Construction companies (EPCs) have relied on highly complex and interactive workflows to execute capital projects. The entire process is very time consuming, and the final deliverable to the Owner Operator is a set of several documents (P&IDs, datasheets, 3D model, etc.) with dispersed data and no guarantee of validity or consistency. But, there is a new way. Today’s EPCs can leverage an integrated engineering and design approach to not only manage, but greatly reduce the overall complexity of engineering and managing engineering data on capital projects. We call this approach Unified Engineering.
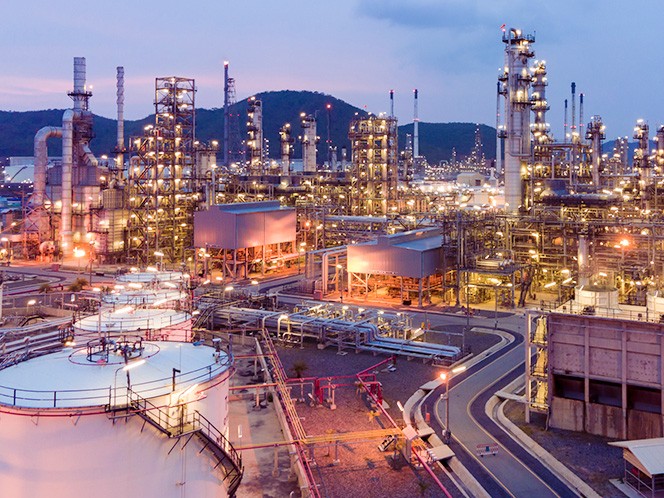
Discover the Unified Engineering Approach
Minimize risk and maximize ROI on your Capital Projects.
Unified Engineering
New technology enables the workflow transition from a document-centric to a data-centric approach. This data-centric approach focuses on keeping the data correct and then updating the documents and applications. Using the data-centric approach is the basic requirement to evolve to a Unified Engineering workflow, allowing EPCs to develop the plant Digital Twin.
This goes beyond the integrated engineering platforms adopted by some EPCs. AVEVA™ Unified Engineering uses a truly single source of data for all the disciplines, so all process simulation, line lists, flowsheets, datasheets, 3D models, isometrics, etc. are updated by the same data bank, configuring your Digital Twin in real-time. Multi-discipline engineers can work concurrently from this single database where all documents and models are automatically updated as soon as any changes are made. They will never need to raise the question if data is correct or not, they can trust the information they are handling.
AVEVA Unified Engineering can help minimize risk and maximize return on capital employed (ROCE), saving up to 30% of engineering efforts during the Engineering and Design phase and enabling further benefits in future phases of the project to ensure lower total installed cost (TIC) overall.
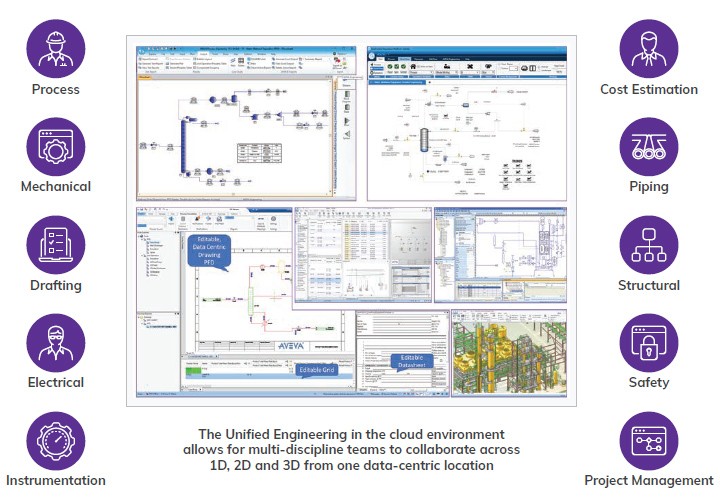
A Digital Twin begins with Engineering
When the Digital Twin is fully developed in the Engineering and Design phases, it becomes a valuable deliverable to the plant’s Owner Operator. Firstly, to understand how the plant was built, it is no longer necessary to look at several different documents or systems because the Digital Twin contains all the relevant information. Secondly, by having all the information in one single environment, maintaining it is much easier. The Digital Twin is kept alive by always containing the most up-to-date information of the plant.
Next step after the plant start-up is to have the online Digital Twin. Then, besides process, equipment and piping data, the Digital Twin can incorporate real-time operational data and information. This type of visibility provides the right context, so engineers and leaders can make better decisions.
In operations, the Digital Twin can be the single source of truth to many applications in the plant, such as operator training simulator, real-time optimization, predictive analytics with machine learning, equipment performance monitoring, etc. Plant owners can benefit by having:
- Reduced unplanned shutdowns;
- A better understanding of equipment issues and root causes;
- An empowered team for better and faster decisions;
- Visibility of optimization opportunities to improve margins;
- Increased safety;
- New technology to attract the next generation of ‘tech savvy’ engineers to traditional industries.
Read the Unified Engineering whitepaper to discover how aligning your teams around a single source of trusted engineering data can fuel your Digital Twin journey.
Related Blog Posts
Stay in the know: Keep up to date on the latest happenings around the industry.