Intelligent pipeline operations
Get the digital tools you need for secure, reliable pipeline operations for liquids, natural gas, petrochemicals, CO2 and hydrogen. Designed for liquid and gas operations, advanced leak detection, and training simulation and visualization, our solutions include the world’s most trusted pipeline SCADA, a comprehensive operational data management system, and a variety of pipeline applications to your operations more efficient and compliant.
"The use of the AVEVA portfolio including the AVEVA™ PI System™ & AVEVA™ Enterprise Pipeline Management Solutions (ePLMS) suite is transforming the way we work, from being reactive to proactive exception-based operations.”
— Matthew Richardson, Leak Detection and OT Engineer, Plains All American Pipeline
Run intelligent pipeline operations with AVEVA Enterprise SCADA and AVEVA PI System
- Natively integrate pipeline SCADA with AVEVA PI System for quality and extensibility.
- Aggregate and contextualize raw field data from control and non-control sources.
- Create custom AVEVA™ PI Vision dashboards with SCADA data.
Learn how Plains All American Pipeline empowered pipeline operators with self-serve analytics.
Build best-in-class control rooms designed for safety, security and compliance
- Lower your total cost of operation (TCO) with re-architected solutions that are easy to upgrade and deploy.
- Use out-of-the box ASM/API-1165 compliant HMI graphics, alarm handling, and no/low-code automation.
- Rely on industry-leading security with defense-in-depth, Purdue ICS model architectures, and ISASecure® SDLA and ISO/IEC27001 certified development.
Learn how a major pipeline operator cut SCADA implementation time by 50%.
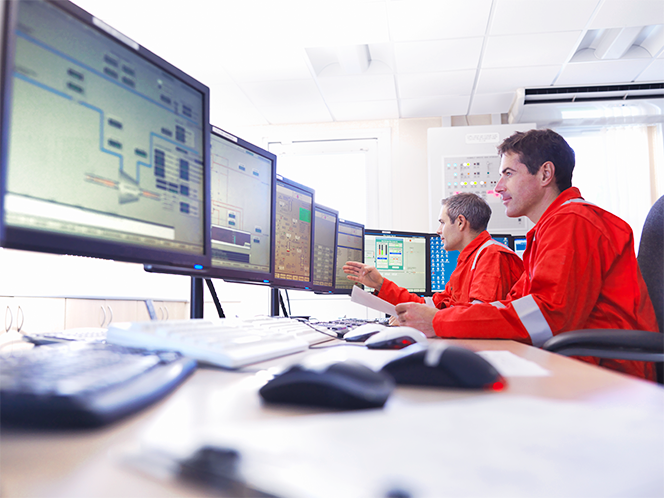
See pipeline data in context with AVEVA PI System
- Contextualize data streams with asset-based configuration of streaming analytics, events and notifications.
- Scale templates quickly across sites while maintaining asset and data hierarchy.
- Securely share operational and environmental data with partners with CONNECT.
See how TC Energy used AVEVA PI System to categorize, maintain and scale its pipeline data.
Improve operations with liquid and gas applications, advanced leak detection, and gas measurement and forecasting
- Determine best efficiency points (BEP) for pumps and optimal drag-reducing agents (DRA) and energy use in liquid pipelines.
- Anticipate leaks with advanced leak detection based on computational pipeline monitoring (CPM) and API RP 1130 standards.
- Accurately measure gas flows and perform advanced gas day forecasting.
Learn how you can keep pace with evolving leak detection regulations.
Empower your business with decision support, next-gen visualization and training
- Make data-based decisions using information-rich AVEVA™ PI Vision dashboards.
- Get a unified, end-to-end view of your pipeline operations.
- Train operators and assess competence with simulators featuring realistic control room systems and hydraulics.
Learn how AVEVA™ Unified Operations Center for Midstream can unify ET, OT, and IT data to drive business value.
AVEVA products for the pipeline economy
AVEVA™ PI System™
Collect, aggregate, and enrich real-time operations data for immediate problem-solving and easily deliver formatted data to enterprise applications and advanced analytics.
AVEVA Enterprise SCADA
Formerly Known As OASyS
AVEVA™ Enterprise SCADA, an enterprise pipeline management system, is the foundation for real-time pipeline operations optimization from edge to enterprise.
AVEVA Pipeline Operations for Liquids
AVEVA Pipeline Operations for Liquids provides everything needed to efficiently manage real-time control room operations and provides liquids and gas operations visibility.
AVEVA Pipeline Integrity Monitor
Prevent, detect and mitigate pipeline commodity releases with multiple leak detection methods in a single application.
AVEVA Operational Safety Management
AVEVA Operational Safety Management enables asset operators to eliminate, minimize, or mitigate operational risk while optimizing asset performance.
AVEVA™ Unified Operations Center for Midstream
Proactively resolve abnormal events for oil and gas pipeline operations management, preventing disruption of production, and integrating with digital safety management systems making operations safer, more sustainable, and efficient through a single pane-of-glass
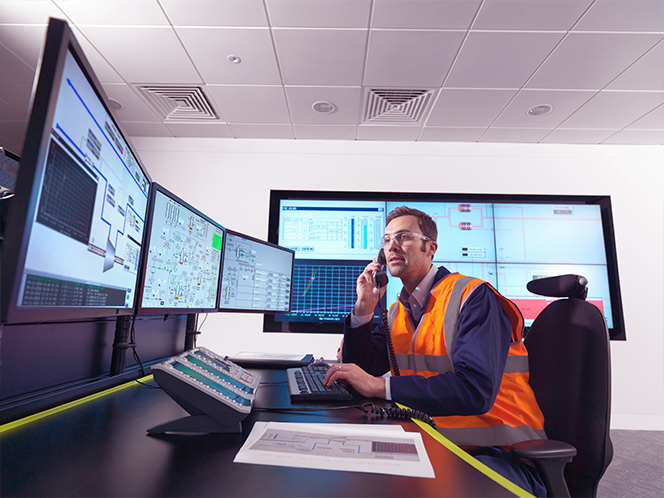
Learn how to stay competitive and profitable in a rapidly changing energy market
Leading oil, gas and energy companies across the globe optimize their plant life cycle for a safer, sustainable future with AVEVA oil and gas software solutions.