CBMM is the world’s leading supplier of niobium, producing about 70-80% of the global supply. Without a system to manage and standardize furnace power curves, operators at CBMM had to rely on their own judgement and intuition, which often led to wasted energy and resources, scrapped products, and equipment failures.
With just its existing AVEVA investments and the expertise of system integrator IHM Stefanini, the team built a new system to implement, standardize, manage, and automate power curves across furnace operations. The new system has already helped CBMM reduce energy use, cycle times, safety risk, and operating costs.
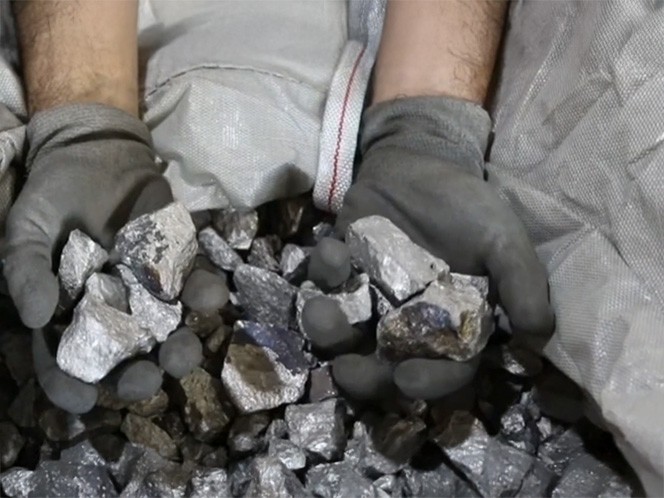
Challenges
Needed a system to improve power curve management and energy efficiency
Lacked standardization and guidance in electric arc furnace operations
Manual processes led to errors, inefficiency, and safety hazards
Results
5.5%
Energy use reduction in one furnace
US$140,000
Annual savings in energy efficiency gains across three furnaces

Improved efficiency and safety
7%
Reduction in cycle time
The world’s leading supplier of niobium
When just a small amount of niobium—no more than 0.1%—is added to steel, that steel (now called high-strength low-alloy steel, or HSLA steel) is made as much as 30-50% stronger at no added weight. The metal also happens to be highly resistant to heat, oxidation, chemical attack, and, at cryogenic temperatures, it’s superconductive. These remarkable properties make niobium very valuable in many different industrial sectors and applications, from renewable energy projects, skyscrapers, bridges, and pipelines to consumer electronics, magnets in MRIs, jet engines, rocket thrusters, and particle accelerators.
Though you’ll find niobium in countless industrial and consumer products, when it comes to finding niobium ore, you’ll have to go to Brazil, where about 98% of the world’s niobium reserves are located. It’s also where you’ll find CBMM (Companhia Brasileira de Metalurgia e Mineração), the world’s leading supplier of niobium, responsible for delivering 70–80% of the global supply.
A new standard
After it’s mined, homogenized, and concentrated, niobium ore must be refined, which is where CBMM’s digital transformation project begins, specifically in the dephosphorization refining plant. Dephosphorization is one of the most essential steps in the production process, and one of the most energy intensive. The process requires a specialized electrical arc furnace and multiple types of energy consumption, including electrode and electrical energy, charcoal, and LP gas. Before CBMM’s digital transformation project, its dephosphorization operations lacked one crucial element: standardization.
Without standardization, operators have no set pattern that tells them exactly how much power to apply to the furnace. Instead, they rely on experience, intuition, and guesswork. Use too little power, and you risk incomplete processing and inconsistent, subpar quality, which can lead to rework, scrapped products, waste, and delays; use too much power, and you risk wasted energy, higher costs, equipment strain, or worse. “When we’re talking about furnaces,” says Amanda Branco, Production Engineer at CBMM, “if you put in a lot of energy when you don’t need it, it could be catastrophic.”
This is where IHM Stefanini, a Brazil-based system integrator, and AVEVA enter the story. With IHM Stefanini’s expertise and CBMM’s existing toolset of AVEVA solutions, the team built a new system to implement, standardize, and manage power curves across CBMM’s furnace operations.
Solution
Used AVEVA™ PI System™, AVEVA™ Production Management, and AVEVA™ InTouch HMI to develop a power curve solution that standardizes and automates furnace operations
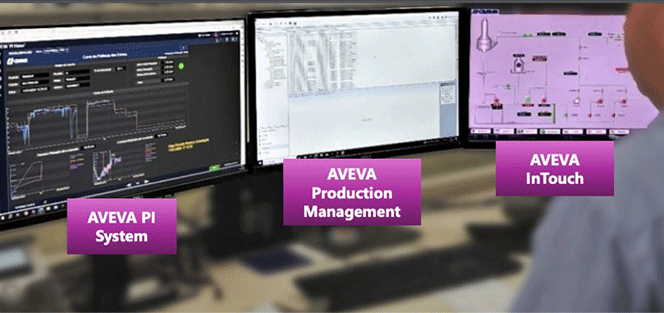
Turning existing investments into new solutions
At the outset, IHM Stefanini took stock of the AVEVA solutions CBMM already used: AVEVA PI System, AVEVA InTouch HMI, and AVEVA Production Management. “What we had to do,” says Moacyr Junior, Digital Manufacturing Leader at IHM Stefanini, “was divide and assemble these pieces—to integrate this puzzle for this problem.” Together, they had to decide: What features would CBMM’s new power curve system need, and which of CBMM’s existing AVEVA software solutions could best deliver those features?
Once the design was mapped out, the team began building an integrated system that would fully leverage CBMM’s existing AVEVA investments—each solution playing a distinct role in defining, executing, and monitoring the power curves. Using AVEVA Production Management, the system defines power curve recipes across refining phases, ensures recipe traceability, and consolidates related production metrics to calculate recipe adherence. Next, with AVEVA PI System, CBMM gathers real-time production data and calculates metrics to track the actual power curve and its alignment with the reference curve. Finally, AVEVA InTouch HMI serves as the PLC interface, managing the download and execution of the power curve recipe.
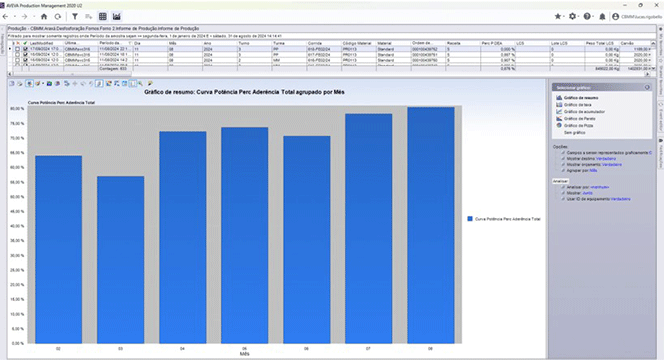
Together, these three solutions enable CBMM to standardize and implement power curves while also executing, controlling, monitoring, and automating furnace operations. “Now, our operators don’t need to change the power manually,” says Amanda Branco. “The system does it itself.” By removing the guesswork from furnace operations, the new system not only reduces energy consumption; it also helps minimize safety risks.
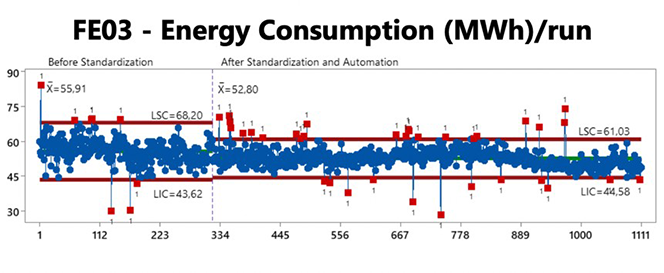
Safer, more energy-efficient furnace operations
With power curves standardized and automated, CBMM has seen marked improvements in the efficiency of each of its three furnaces, especially the newest furnace, Furnace #3. Before CBMM had implemented and standardized power curves, Furnace #3 used 55.91 MWh per run. Now, after implementation, Furnace #3 consumes 52.80 MWh per run. That’s about a 5.5% reduction in energy consumption.
Furnaces #1 and #2 saw approximately 1MWh reduction per run. The energy savings between all three furnaces totals approximately US$ 140,000 annually.
Aside from improving efficiency and safety, the new system has also reduced cycle times by about 7%. “Just because now, we know what we’re doing,” says Amanda Branco. “We can see when we’re doing much better or when we’re doing worse, and then we get a standard. It has been really great for the process.”
“We can see when we’re doing much better or when we’re doing worse, and then we get a standard. It has been really great for the process.”
—Amanda Branco, Production Engineer, CBMM
What’s next for CBMM?
The early success of CBMM’s new power curve solution has the team optimistic about unlocking even greater energy and cost savings. With standardized power curves now in place, the next step is to optimize them using AI-powered technologies. But the benefits extend beyond more efficient furnace operations. “This kind of solution,” says Lucas da Silva Rigobello, System Analyst at CBMM, “that provides standards for our operations and also makes the most of our existing IT and control systems should be replicated across other production processes at CBMM.”
Product highlights
AVEVA™ PI System™
Collect, aggregate, and enrich real-time operations data for immediate problem-solving and easily deliver formatted data to enterprise applications and advanced analytics.
AVEVA InTouch HMI, formerly Wonderware
Formerly Known As InTouch HMI
AVEVA InTouch HMI is HMI visualization software for operators to achieve real-time operations visibility. The world’s most widely used plant HMI for process monitoring and control.
AVEVA Production Management
Formerly Known As Ampla Operations Management
AVEVA Production Management (Formerly Ampla Operations Management) allow you to increase your operational profitability, agility and competitiveness by providing you with end to end process visibility and data driven decision making based on a single trusted source of information.