Are you an AVEVA™ PI System™ customer? Learn how your data can ensure reliable, profitable and sustainable operations.
Visit the dedicated hub.
Rio Tinto streamlines data at every stage of the mining value chain
From pit to port, Rio Tinto’s data infrastructure provides real-time insights across multisite operations. Whether it’s improving engineering and operations or optimizing and modernizing plants, Rio Tinto is connecting the dots across its many sites and projects using data in context.
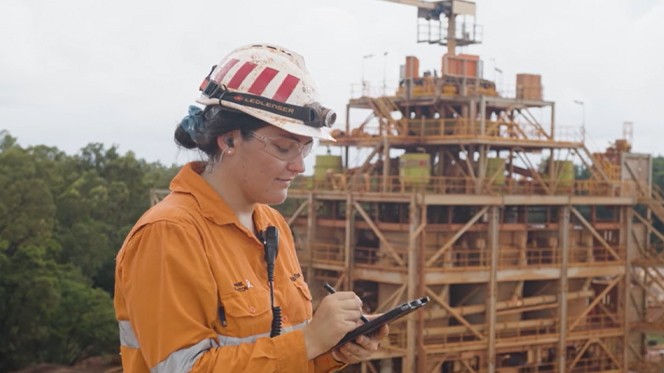
“We’ve improved product quality by 125% through our Digital at Exxaro strategy with AVEVA."
—Pleasure Mnisi, CTO, Exxaro
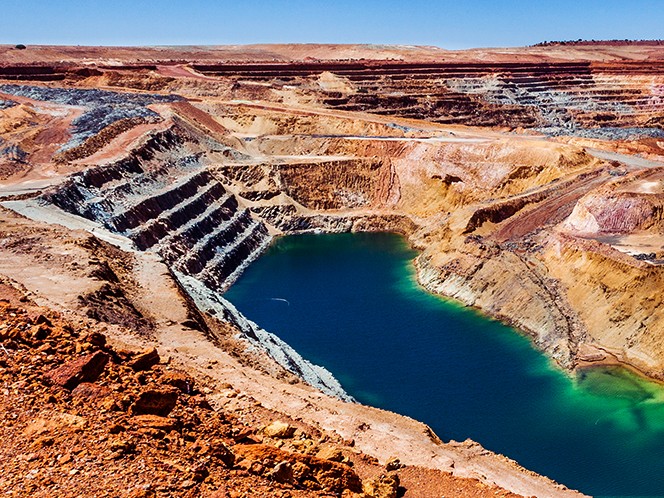
Protect precious resources and lower your carbon emissions
- Better data transparency and visibility lead to safer, more sustainable operations.
- Increase engineering agility for quicker reactions to markets.
- Lower your carbon footprint and comply with ESG targets.
Barrick Goldstrike uses AVEVA™ PI System™ to manage its mining data and automate environmental regulation compliance reports.
Shorten engineering cycles
- Lower CapEx and OpEx with more efficient engineering cycles.
- Execute mining projects faster to deliver products more quickly.
- Collaborate with teams and partners in the cloud.
See how K+S Potash increased project execution agility and made information handover to owner-operators more efficient.
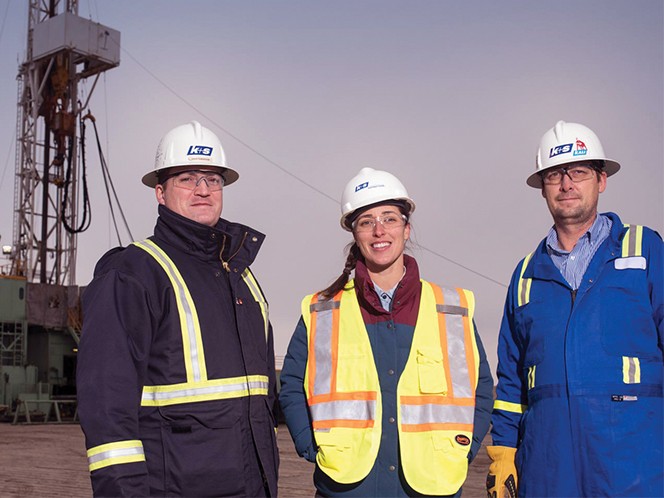
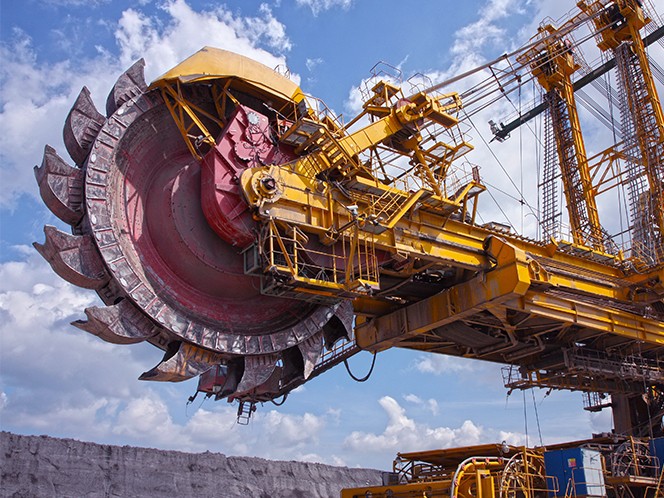
Optimize the entire value chain and increase productivity
- Improve production with short interval control methods and master data management.
- Balance supply and demand with better planning.
- Make reliable forecasts to maximize recovery.
See how MMG Limited increased asset utilization by 10% across its sites.
Make your assets safe, more efficient, and more reliable
- Predictive maintenance strategies minimize unplanned downtime and extend your asset lifecycle.
- Improve situational awareness for safer operations.
- Increase asset performance and efficiency to reduce maintenance costs.
See how Lonmin Mining Co. increased its operational efficiency by 10%.
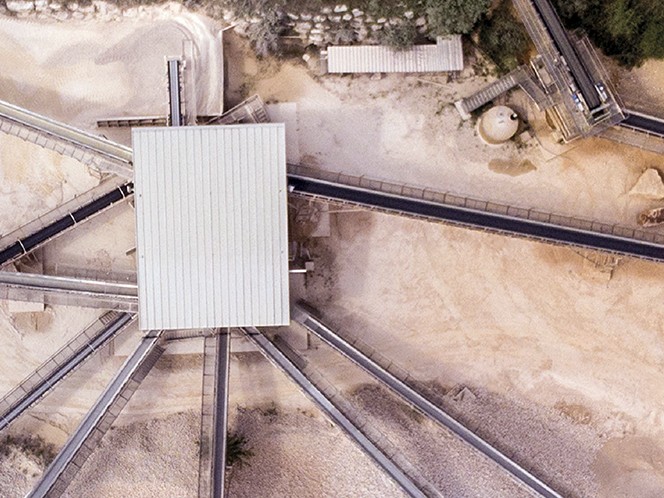
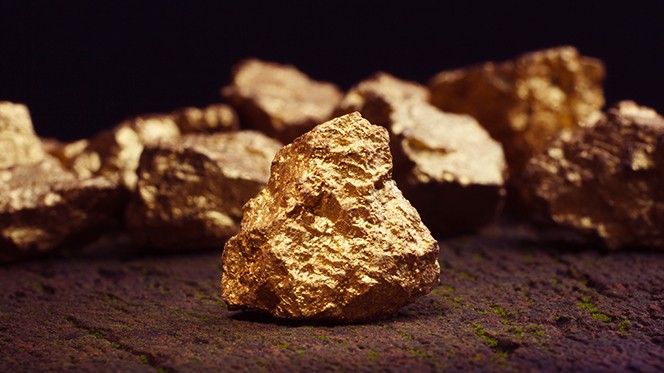
Make improvements across the entire metals value chain for better productivity
- Improve production with short interval control methods and master data management.
- Refine processes to increase throughput, yields, and product quality.
- Stabilize critical equipment operation to reduce energy consumption.
See how Aurelia Metals increased its gold recovery rate from 62.1% to 88.6% and saved $250,000 in manufacturing costs.
AVEVA products for the mining economy
AVEVA™ PI System™
Collect, aggregate, and enrich real-time operations data for immediate problem-solving and easily deliver formatted data to enterprise applications and advanced analytics.
AVEVA™ Unified Engineering
AVEVA Unified Engineering is a data-centric engineering environment. Engineer and collaborate across all project phases and multi-discipline teams in real time.
AVEVA Production Management
Formerly Known As Ampla Operations Management
AVEVA Production Management (Formerly Ampla Operations Management) allow you to increase your operational profitability, agility and competitiveness by providing you with end to end process visibility and data driven decision making based on a single trusted source of information.
AVEVA Predictive Analytics
Formerly Known As PRiSM Predictive Asset Analytics
End unplanned downtime and reduce maintenance costs with accurate asset health information that improves operating efficiency and resilience
AVEVA™ Unified Operations Center
Converge engineering, operations and other data in context for end-to-end enterprise visibility
AVEVA™ Asset Information Management
Accelerate information discovery and break down silos for fast, intuitive, in-context access to relevant data.