Three things you can do to get value from your smart factory
Posted: January 11, 2024
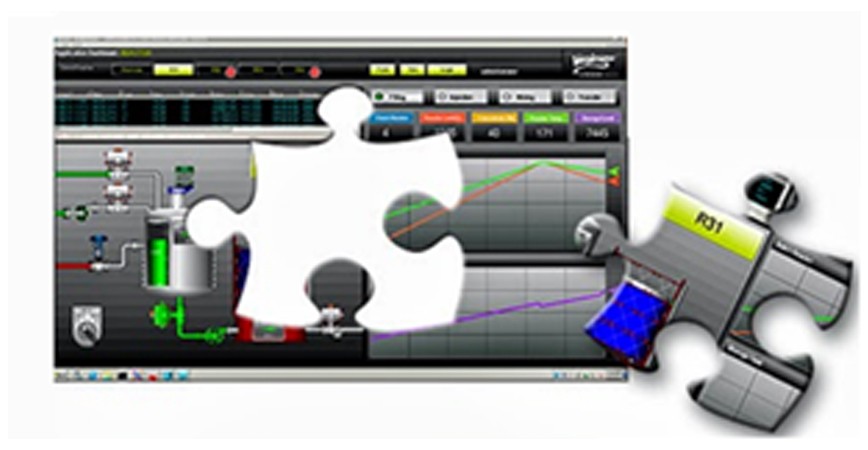
Since it was defined by the Industry 4.0 Working Group in 2013, the concept of the “smart factory” has become increasingly sought after as a technological panacea to address the challenges of operational disruptions for manufacturers.
A quick google of “smart factory” yields over a billion results, many of them, to be fair, from technology companies like AVEVA. A 2022 article by Forbes suggested that 74% of manufacturers have smart factory initiatives underway, with an expected ROI of $500B-$1.5T. Yet only 14% of those manufacturers were satisfied with their level of accomplishment to date, well and truly putting the smart factory in the “Trough of Disillusionment” in the Gartner Hype cycle.
Given the level of interest and investment in the smart factory concept, what is the missing piece, or pieces, that cause these initiatives to stall? Below I’ll discuss three strategies that can help to maximize the success and value of your smart factory initiative.
Create a data foundation
The first and most critical step is to design and create a data foundation for your smart factory. Manufacturing plants are already awash in data—that data is just tightly locked into various silos (automation, HMIs, historians). So, the first step is to design a data architecture, one that can accommodate data from your existing OT systems and is also flexible enough to accommodate additional data streams and types that come from IIoT sensors, smart devices and other systems.
Ideally, this architecture will be tiered to isolate real-time and production systems from analytic and reporting data sets, so that using one won’t impact the other. Cloud is typically an excellent choice for the higher tiers of this architecture, as it can be scaled to accommodate enormous amounts of data and cross geographic boundaries, while remaining secure and easy to manage. But more on that when I talk about scalability.
Connect it to your operating model
The second step seems obvious but often goes awry. The goal of the smart factory initiative is always to improve the performance of the factory. Improving factory performance is a balance of digitizing existing processes and activities, with new automation and improved processes. Lean thinking is a good guide here. Take a process-based approach to look at what adds value and how to reduce waste; make decisions around what can be automated and define best practices to improve the work people are doing. The “start small, fail fast” mantra can be helpful here, with a phased approach to rolling out changes to the plant. However, beware of proliferating multiple “atomic” tools that can only ever address a part of the capabilities you need. These solutions can create new silos of data and add redundant points of configuration and maintenance.
A better approach is a modular, process-based MES that can address the full range of manual or automated processes. This approach provides a single version of truth and point of configuration and allows you to manage the entire lifecycle of the plant. These modern MES solutions can best align to your desired operating model and provide a solid basis for change management and continuous improvement within the plant.
Make it scalable
There are really three aspects to consider around scalability. The first is standardization. To truly deliver value, a smart factory initiative needs to span fragmented manufacturing networks. This often means a lighter deployment at smaller, less mature plants, with a broader end-to-end deployment at the larger and more business-critical plants. It takes work up front to understand the diversity across your network. However, this standardization also presents an opportunity for SMEs to design the best practices that account for the unavoidable variations between sites, while eliminating those that are unnecessary. The digital systems within your plants need to be able to support both the standards and the adaptability of local variations.
The second area of value comes from leveraging the scale of your manufacturing network for smart manufacturing. Standardizing the digital footprint of the plants and how they interoperate with your supply chain systems opens up many potential new use cases for better visibility, collaboration and planning capabilities across plant operations, creating a more agile and resilient supply chain.
The final aspect of scalability is cost of ownership. To be successful in your smart manufacturing journey, the cost and time to deploy smart factory initiatives across multiple plants must decrease per plant deployed. There are several things to consider regarding technology when looking at these costs. You should explore contemporary architectures such as managed edge applications, low code/no code, and single MES instance/multi-site deployments, along with the tools available for change management and governance of the best practices. Cloud can also play a key role in reducing TCO as mentioned earlier, particularly for data management and the information-centric aspects of operation, such as dashboards and reporting.
The smart factory is also a key component and enabler of the connected industrial economy I talked about in my last post, a concept that was quite prophetically described in the “Final report of the Industry 4.0 Working Group” in 2013 as the “Internet of Things and Services.” The concept of the connected industrial economy adds an entirely new level of return on your smart factory investments, making it even more imperative to succeed in these programs.
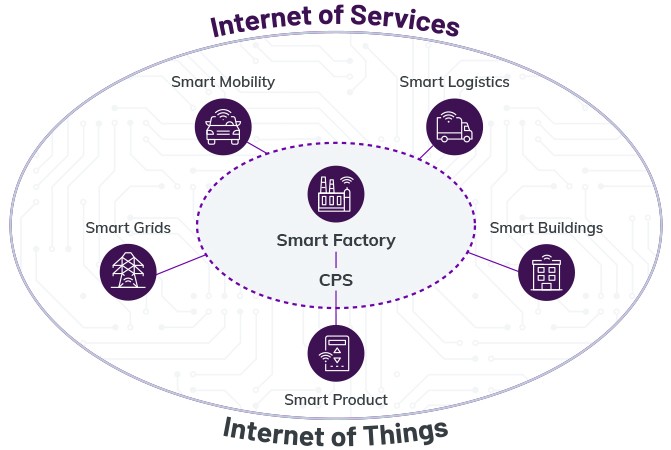
There are of course no guarantees in the smart factory business, so choose your partner carefully. Choose a partner who understands your business and the processes and pain points within your plants, one who can support your initiative across your entire manufacturing network. Finally, choose a partner who has proven technology and a commitment to ongoing investment in transformational technology like cloud, AI and augmented reality. In my next post, I’ll dive into the digital thread and how it connects customer demand through the smart factory, back to that customer, and lines up with the three points I outlined above.
If you’d like to dive into the benefits of using a single MES instance/multi-site operations deployment architecture, check out our infographic around how to “Lower the cost and complexity of MES standardization”.
Related blog posts
Stay in the know: Keep up to date on the latest happenings around the industry.