SCADA vs HMI: The difference between them
Posted: 16 March, 2021
Are HMI and SCADA related to each other? How?
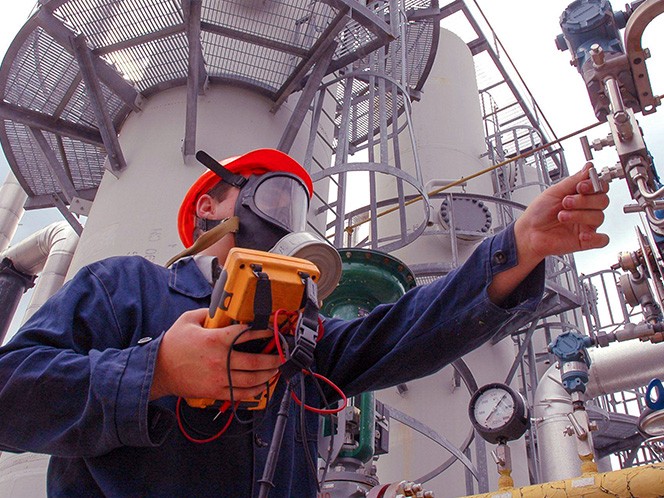
What is the difference between SCADA and HMI?
HMI and SCADA software two terms for distinct industrial automation interfaces. HMIs are subsets or components of a SCADA system. Additionally, a DCS or Distributed Control System is very similar to a SCADA system, and may also use one or more HMIs as well. All these components are classes of, or describe parts of, an ICS or Industrial Control System, which is the general description of Automation. In modern control systems, there is a great deal of overlapping technology and functionality between these two classes of ICSs.
What is HMI?
HMI or Human Machine Interface is simply the way by which humans interact with machines. An HMI in terms of the AVEVA Edge platform is a control panel that is easily designed, implemented, and maintained/modified simply by creating or modifying it in the AVEVA Development Environment. Using AVEVA Edge SCADA/HMI software to design HMIs can save months of development, rework, and rewiring time over creating (a) hard-wired control panel(s) or machine interface panel(s). Software HMIs will securely operate in runtime on a host machine (application server) or as a Thin Client using Microsoft® Internet Explorer or in AVEVA’s Secure Viewer on a variety of displays or multi-displays, devices, and platforms as a built-in interface, a portable interface, or a handheld interface and display terminal. HMIs can also be remotely accessed and controlled over the web with secure configurations. For example, AVEVA Edge follows HTML5 standards, and can be fully accessed via a browser.
What is SCADA?
A SCADA (Supervisory Control and Data Acquisition) System is an Automation or Industrial Control System that may involve, directly control, or communicate with one or more of the following:
- Networked industrial automation and machines
- Remote telemetry and control using continuous or burst communications
- Process Control and Statistical Process Control systems
- Data Acquisition Systems (DAQs)
- Historians and Data Storage Servers
- Industrial Control Systems utilizing PLCs and RTUs.
- Business environment systems such as ERP4 and MES5 Systems.
- Industrial Cloud Computing Environment
- Security Systems and Processes
- local machine security or
- process security and control
- Enterprise or global level involving LDAP and other connectivity.
A SCADA system may be continuously connected to all the components in the ICS, or may be intermittently connected to some or all, and updated with a burst communication over radio or cellular modems (2G, 3G, or 4G, CDMA, and GSM technologies) to field devices and equipment. A SCADA system usually has a one or more SCADA Servers containing an application that is/are communicating with and running in conjunction with intelligent single-purpose intelligent components such as PLCs and/or RTUs, or possibly even remote, independent SCADA systems. AVEVA Edge serves as a SCADA software platform on which to design an effective SCADA system.
An Industrial Control System as described may be connected together via (one or more of the following) serial connections, proprietary and/or Ethernet network, LAN, WAN, and/or Cloud and may involve widely dispersed external components and/or facilities; include processes such as MES and ERP Systems, Process Control and Data Historians, JIT and other upstream/downstream manufacturing connectivity, etc.
A DCS or Distributed Control System is similar to, and in some cases, can be indistinguishable from, a SCADA system but is generally considered to be a more self-contained process control type of automation. A DCS usually has a Control Server hosting the Supervisory Control System with the possibility of various SCADA Servers and/or Master Terminal Units or Master Telemetry Units (MTUs) communicating with PLCs, RTUs, Process Historian and/or other business entities as discussed in SCADA systems. DCSs can also be used in Continuous and Batch-based Process Control and may or may not have proprietary components throughout the whole system.
HMIs, SCADA, and Control Systems developed using AVEVA Edge SCADA/HMI software are used within many types of vertical industries, large and small, in order to provide a means of direct process and machine control, automation, security, data storage and analyses, indirect operation services such as ingress/egress control, communications and video; and connectivity to a variety of functionality within the system or manufacturing and supply chain that may be closely or loosely associated with the operational or manufacturing of those products and services.
Related Blog Posts
Stay in the know: Keep up to date on the latest happenings around the industry.