Danone, a core MES model for global rollout
Danone developed its DANMES solution using a templated approach with 15 standard functions (including a standard interface to SAP) to facilitate deployment across the whole business, starting with its Specialized Nutrition division.
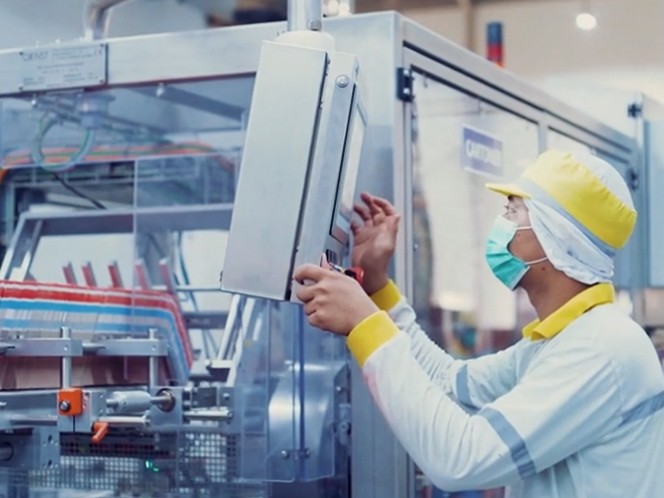